리소그래피 기계는 칩 제조에서 가장 복잡하고 값비싼 장비입니다. 칩 제조에는 예비 산화, 포토레지스트 코팅, 노광, 현상, 에칭, 이온 주입과 같은 여러 공정이 포함될 수 있습니다. 이 공정에는 산화로, 접착 및 현상 기계, 리소그래피 기계, 박막 증착 장비, 에칭 기계, 이온 주입기, 연마 장비, 세척 장비 및 테스트 장비를 포함한 다양한 장비가 필요합니다. 전체 반도체 칩 제조 공정에서 리소그래피는 가장 복잡한 공정이며, 리소그래피 공정 비용은 칩 제조 비용의 약 1/3을 차지하고, 시간 소비는 약 40-50%를 차지하며, 리소그래피 공정에 필요한 리소그래피 기계는 가장 비싼 반도체 장비입니다.
리소그래피 기계는 프론트 엔드 리소그래피 기계와 백엔드 리소그래피 기계로 나눌 수 있습니다. 리소그래피 기계는 프론트 엔드 공정 및 백엔드 공정에 사용할 수 있으며, 프론트 엔드 리소그래피 기계는 칩 제조에 사용되며, 노광 공정은 매우 복잡하고, 백엔드 리소그래피 기계는 주로 고성능 고급 패키징을 달성하기 위한 포장 및 테스트에 사용되며 기술적 어려움은 상대적으로 작습니다.
그림 1: 리소그래피 공정 흐름도
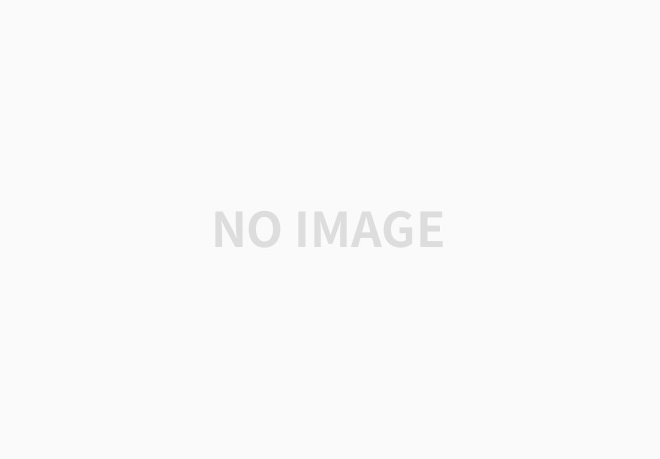
데이터 출처: 리소그래피 기계 산업 보고서, Zhongtai Securities Research Institute
리소그래피 기계의 개발이 어렵고, 부품이 해외에서 독점되고 있습니다.
그림 2: 세계 5대 반도체 장비 제조업체의 R&D 비용 비율
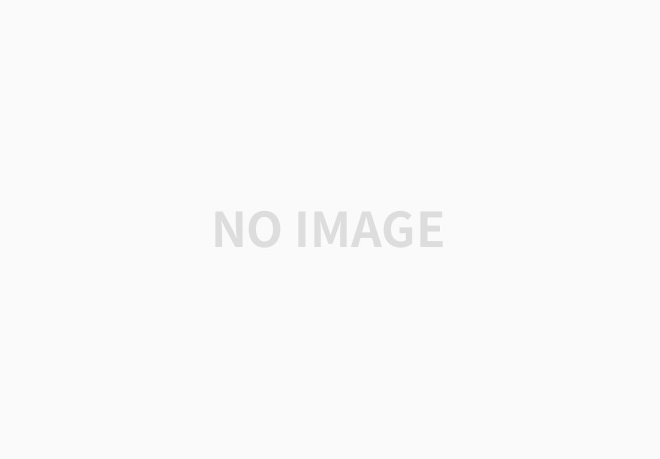
데이터 출처: 리소그래피 기계 산업 보고서, Zhongtai Securities Research Institute
리소그래피 기계 제조업체의 높은 R&D 비용 비율: 22년 동안 세계 5대 반도체 장비 제조업체의 평균 R&D 비용 비율은 11%이며, 그 중 ASML의 R&D 비용 비율은 15%로 다른 장비 제조업체보다 높습니다.
리소그래피 기계 부품 공급업체는 전 세계에 있으며 핵심 부품은 독일과 미국에서 생산됩니다: 리소그래피 기계의 가장 첨단 기술을 대표하는 EUV 리소그래피 기계는 전 세계적으로 100,000개 이상의 부품 및 부품과 5,000개 이상의 공급업체를 보유하고 있습니다. 전체 리소그래피 기계에서 네덜란드 캐비티와 영국 진공이 32%, 미국 광원이 27%, 독일 광학 시스템이 14%, 일본 재료가 27%를 차지했습니다.
그림 3: EUV 리소그래피 기계 구성 요소의 비율
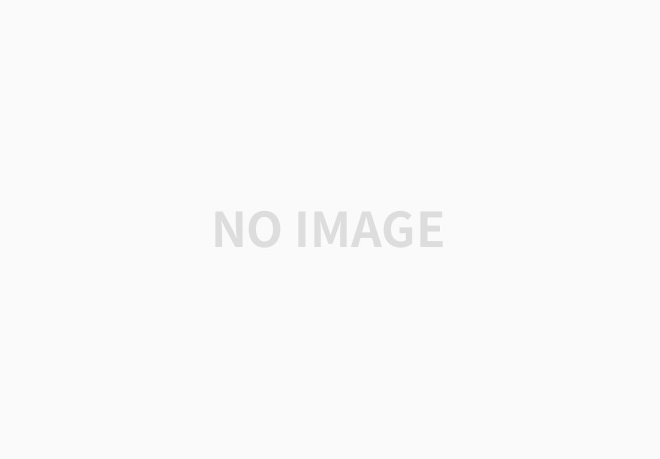
데이터 출처: 리소그래피 기계 산업 보고서, Zhongtai Securities Research Institute
리소그래피 장비의 단가가 가장 높고 시장은 세계에서 두 번째로 큽니다.
2021년 글로벌 프론트엔드 리소그래피 장비 시장 규모는 172억 달러였으며 웨이퍼 생산 장비의 시장 점유율은 20%를 차지하여 에칭 장비에 이어 두 번째입니다. 리소그래피 기계는 비싸고 ASML의 현재 EUV 리소그래피 기계 단가는 1억 5천만 달러에서 2억 달러입니다.
별첨 4: 글로벌 반도체 제조 장비 시장 점유율
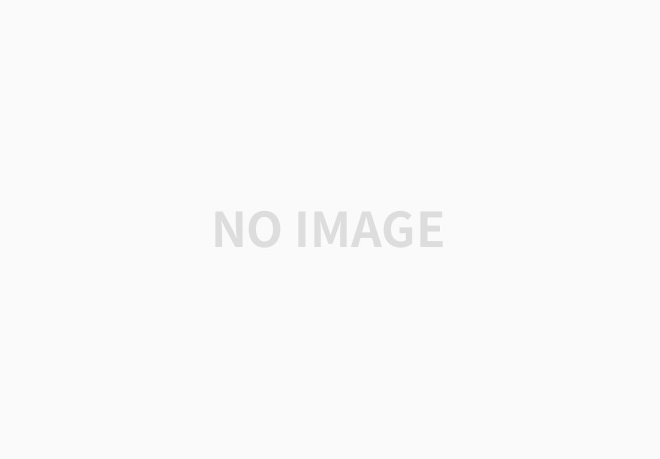
데이터 출처: 리소그래피 기계 산업 보고서, Zhongtai Securities Research Institute
MOSFET에 비해 IGBT는 더 높은 전압에서 계속 작동할 수 있으며 동시에 높은 전력 밀도, 낮은 손실, 높은 신뢰성, 우수한 방열 및 저렴한 비용과 같은 요소를 고려해야 합니다. 고성능, 고신뢰성 및 저비용 IGBT 칩은 설계 단계에서 장치 구조를 지속적으로 최적화해야 할 뿐만 아니라 웨이퍼 제조 및 패키징에 대한 더 높은 요구 사항을 제기합니다.
그림 5: 2021년 웨이퍼 생산 장비 시장 점유율
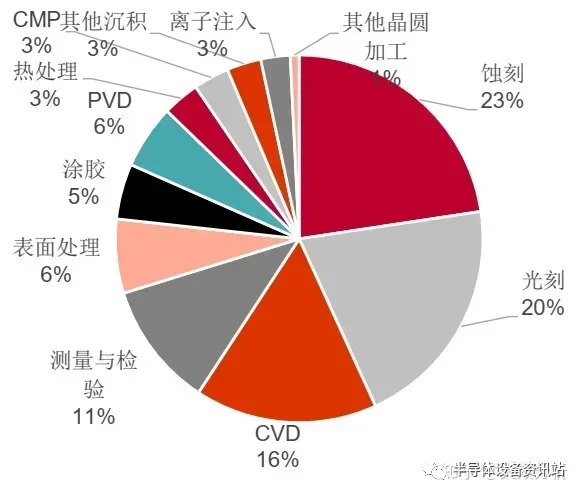
데이터 출처: 리소그래피 기계 산업 보고서, Zhongtai Securities Research Institute
접촉식에서 EUV에 이르기까지, ASML은 절대적인 리더가 되었습니다
1961년 미국 GCA에 의해 최초의 접촉식 리소그래피 기계가 출시되었으며, 60년의 개발 끝에 ASML은 현재 리소그래피 기계 산업의 절대적인 리더가 되었습니다.
리소그래피 기계: 1955년 Bell Labs는 리소그래피 기술을 사용하기 시작했으며 1961년 GCA는 최초의 접촉식 리소그래피 기계를 제작했습니다.
단계별 리소그래피 기계 출시 : 1978 년에 단계별 리소그래피 기계가 도입되었으며 1984 년 Nikon과 GCA가 각각 30 %의 점유율을 차지했으며 같은 해 ASML이 설립되었습니다.
침지 리소그래피 기계 출시: 2000년에 ASML은 2단 리소그래피 기계를 출시했으며 2003년에 ASML은 침지 리소그래피 기계를 출시했습니다.
EUV 리소그래피 기계 출시: 2013년 ASML은 세계 최초로 EUV 양산 제품을 출시하며 업계 독점적 지위를 더욱 공고히 했습니다.
그림 6: 리소그래피 기술의 역사
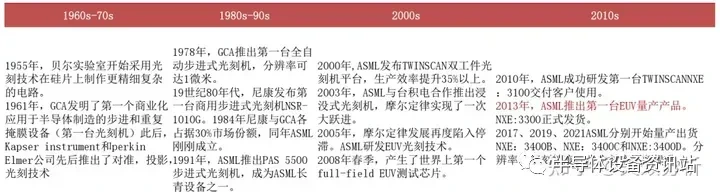
데이터 출처: 리소그래피 기계 산업 보고서, Zhongtai Securities Research Institute
리소그래피: 접촉에서 근접까지
접촉식 리소그래피 기술은 수율이 낮고 비용이 많이 듭니다: 접촉식 리소그래피 기술은 20세기 60년대에 등장했으며 소규모 집적 회로 시대에 가장 중요한 석판인쇄술 기술입니다. 콘택트 리소그래피에서 마스크는 웨이퍼 표면의 포토레지스트와 직접 접촉하고 전체 기판이 한 번에 노출되며 마스크 패턴과 웨이퍼 패턴 사이의 크기 관계는 1:1이며 해상도는 서브미크론 수준에 도달할 수 있습니다.
특징 : 접촉 유형은 빛의 회절 효과를 줄일 수 있지만 접촉 과정에서 웨이퍼와 마스크 사이의 마찰로 인해 흠집이 발생하기 쉬워 입자 염색이 발생하고 웨이퍼 수율과 마스크의 수명이 감소하며 마스크를 자주 교체해야하므로 근접 리소그래피 기술이 도입됩니다.
근접 리소그래피는 해상도가 제한되어 있습니다: 근접 리소그래피는 20세기 70년대에 널리 사용되었으며, 근접 리소그래피의 마스크와 웨이퍼는 포토레지스트가 직접 접촉하지 않아 질소로 채워진 틈을 남긴다는 것을 나타냅니다.
특징: 최소 해상도 크기는 간격에 비례하며 간격이 작을수록 해상도가 높습니다. 단점은 마스크와 웨이퍼 사이의 간격이 빛의 회절을 유발한다는 것이므로, 근접 리소그래피 기계의 공간 해상도 한계는 약 2μm입니다. 피처 크기가 줄어들면서 프로젝션 리소그래피가 등장했습니다.
그림 7: 접촉 리소그래피의 개략도
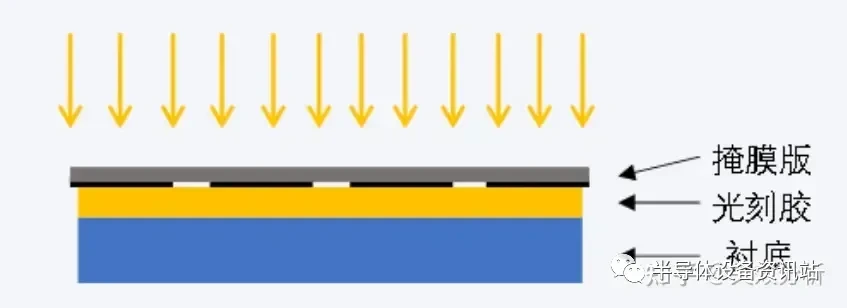
그림 8: Proximity lithography의 개략도
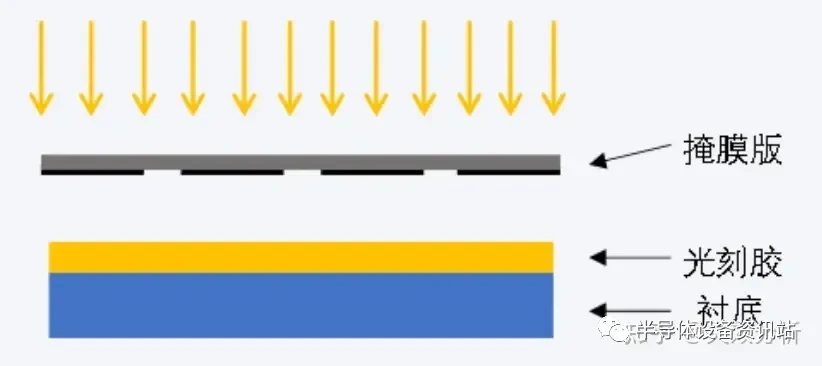
데이터 출처: 리소그래피 기계 산업 보고서, Zhongtai Securities Research Institute
리소그래피: 근접성에서 투영까지
프로젝션 리소그래피 기술의 효과적인 해상도 향상: 20세기 70년대 중후반에 프로젝션 리소그래피 기술이 등장했으며, 원거리 푸리에 광학 이미징 원리를 기반으로 마스크와 포토레지스트 사이에 배율을 줄인 프로젝션 이미징 대물 렌즈를 사용하여 해상도를 효과적으로 향상시켰습니다. 초기에는 기판 패턴 크기에 대한 마스크의 비율이 1:1이었고, 집적 회로의 크기가 지속적으로 축소됨에 따라 배율을 줄인 단계별 반복 리소그래피 기술이 등장했습니다.
스텝 반복 리소그래피는 주로 0.25 μm 이상의 공정에서 사용되며, 리소그래피 중에 마스크가 고정되고 웨이퍼가 스텝되어 모든 노광 작업을 완료합니다. 집적 회로의 통합이 지속적으로 개선됨에 따라 칩 면적이 커지고 단일 노출에 필요한 면적이 증가하여 보다 발전된 스테퍼 스캐닝 리소그래피 기계의 출현을 촉발했습니다. 현재 스텝 반복 리소그래피는 주로 0.25μm 이상의 공정과 고급 패키징에 사용됩니다.
스텝 스캔 리소그래피가 널리 사용됩니다 : 스텝 스캔 리소그래피는 노광 필드 크기 및 노광 균일 성에서 장점이 있으며 0.25 μm 미만의 제조에서 스텝 반복 리소그래피 기계의 사용을 줄입니다. 현재 노광이 완료된 후, 마스크는 전체 웨이퍼가 노광될 때까지 다음 스캐닝 필드까지 노광을 계속 반복한다. 0.18μm 노드에서 시작하여 실리콘 기판의 CMOS 공정에 널리 사용되는 스텝 스캐닝 리소그래피는 7nm 미만의 공정 노드에 사용되는 EUV도 스텝 스캐닝 방법을 사용합니다.
그림 9: 프로젝션 리소그래피 회로도
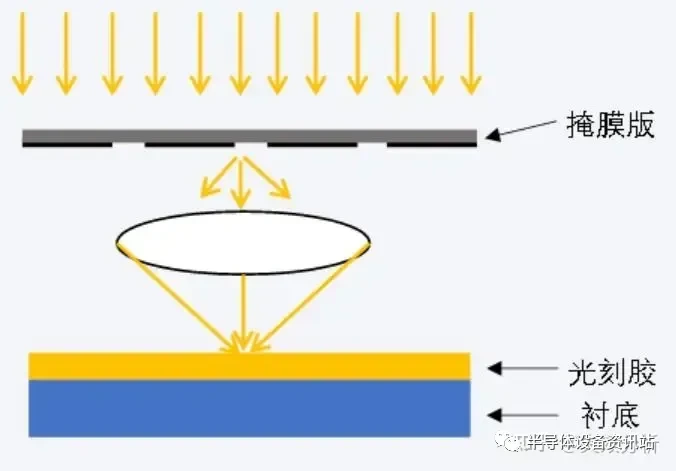
그림 10: 단계별 반복 리소그래피의 개략도
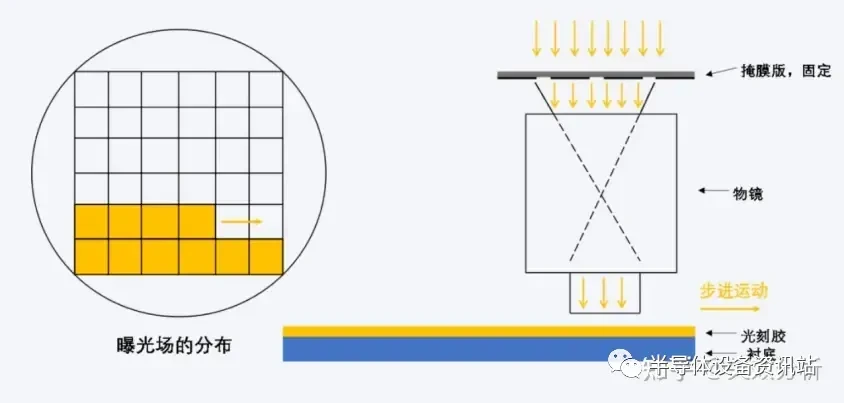
그림 11: step-by-step scanning lithography의 개략도
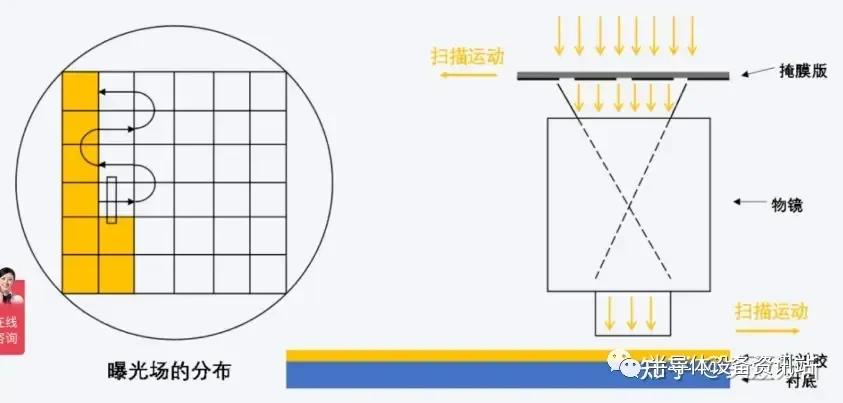
리소그래피 기술: 드라이 리소그래피 및 침지 리소그래피
프로젝션 리소그래피 기술은 프로젝션 대물렌즈 아래와 웨이퍼 사이에 매체로 물이 있는지 여부에 따라 드라이 리소그래피와 이멀젼 리소그래피로 나눌 수 있습니다.
드라이 리소그래피는 계속 줄어드는 선폭을 충족시킬 수 없습니다: 빛은 프로젝션 대물렌즈에서 방출되어 유리 매체에서 공기 매체로 들어가 회절되고 빛의 각도가 변한 후 최종적으로 웨이퍼 표면에서 이미징됩니다. 선폭이 계속 줄어들고 회절 효과가 증가함에 따라 더 많은 빛을 받기 위해 투영 대물렌즈의 직경을 늘려야 하며, 이로 인해 대물렌즈에서 집중된 빛의 각도가 증가합니다.
이멀젼 리소그래피 기술은 리소그래피의 수준을 더욱 향상시킵니다: 프로젝션 대물 렌즈의 바닥과 웨이퍼 사이는 물로 채워져 있고, 물의 굴절률이 유리의 굴절률에 가깝기 때문에(193nm의 파장에서 굴절률 공기 = 1, 물 = 1.44, 유리는 약 1.5), 프로젝션 대물렌즈에서 방출되는 빛은 수성 매체로 들어가고 굴절각이 더 작으며 빛은 대물 렌즈에서 정상적으로 굴절될 수 있습니다. ArF 광원과 침투 기술의 실제 등가 파장은 193nm/1.44=134nm입니다.
그림 11: 드라이 리소그래피의 개략도
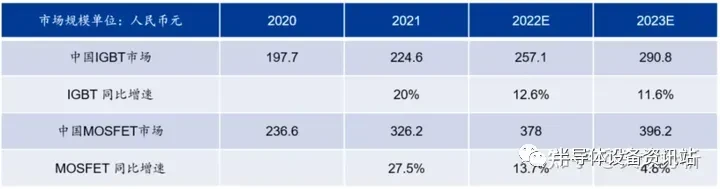
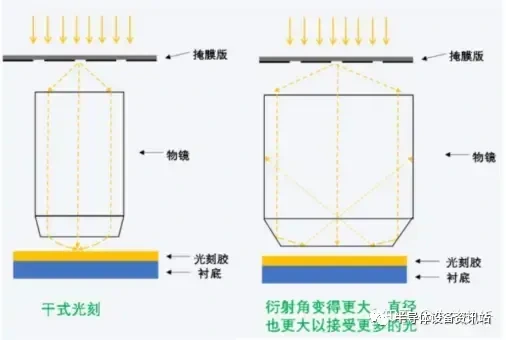
그림 12: 침수 시스템의 개략도
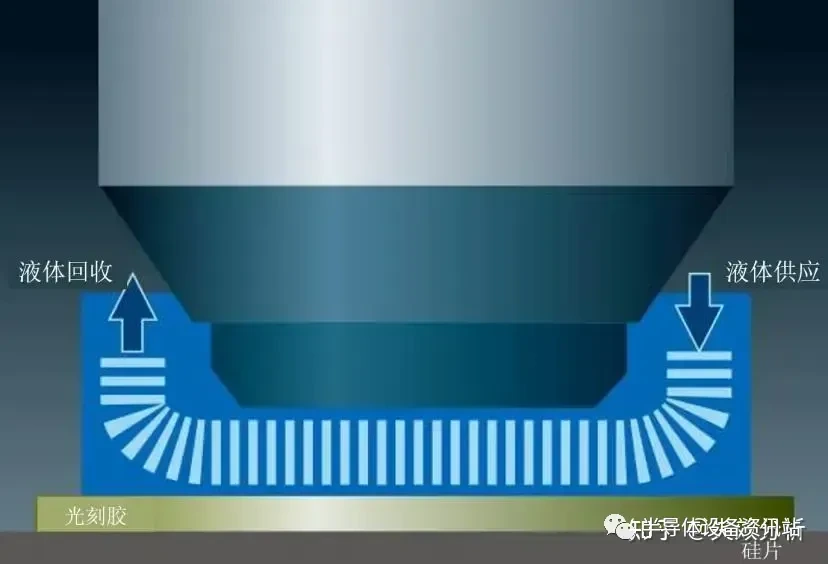
그림 13: 유리, 공기, 물에서 빛의 굴절
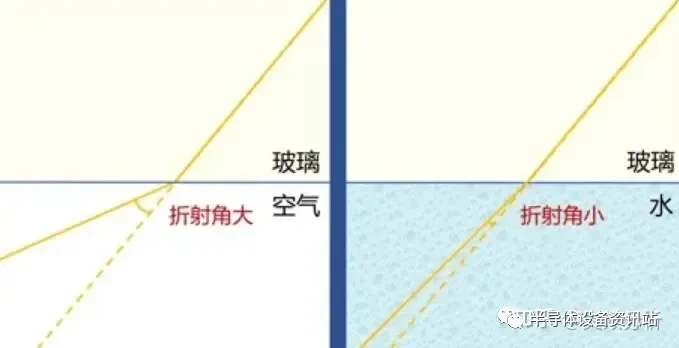
데이터 출처: 리소그래피 기계 산업 보고서, Zhongtai Securities Research Institute
리소그래피 기계의 기술 수준은 집적 회로의 개발 수준을 결정합니다
리소그래피 기계의 기술 수준은 집적 회로의 개발 수준을 크게 결정합니다. EUV 리소그래피 기계의 출현으로 칩 제조 공정은 3nm에 불과했습니다. 현재 ASML은 2nm와 1.8nm 공정의 High-NA EUV 리소그래피 기계를 개발 중이며, 2025년 양산을 목표로 하고 있다. 이와 함께 엔비디아는 23년 GTC 콘퍼런스에서 획기적인 리소그래피 컴퓨팅 라이브러리 쿠리토(cuLitho)를 통해 컴퓨테이셔널 리소그래피를 40배 이상 가속화해 2나노 이상의 첨단 칩 생산을 가능하게 할 것이라고 밝혔다.
그림 14: 공정 노드와 리소그래피의 관계
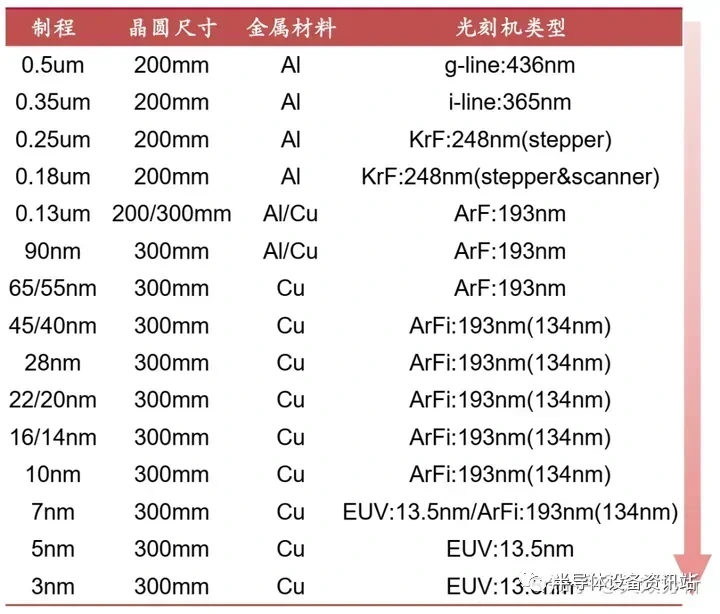
별첨 15: ASML의 고객 노드 진화 예측
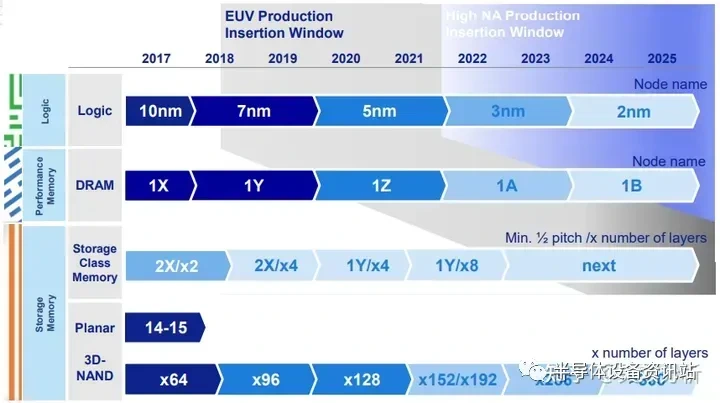
다중 노출은 또한 더 작은 선 너비를 얻을 수 있지만 프로세스는 더 어렵습니다
리소그래피는 더 작은 선 너비를 얻기 위해 여러 노출 프로세스를 사용합니다. LELE, LFLE, SADP 세 가지 다중 노출 기술이 있으며 더 작은 것은 SADP입니다.
1) LELE(LITHO-ETCH-LITHO-ETCH LITHOGRAPHY-ETCHING-LITHOGRAPHY-LITHOGRAPHY-LITHOGRAPHY-ETCHING: 리소그래피의 원래 층을 두 개 이상의 마스크로 분할하고 다중 노출 및 에칭을 사용하여 디자인 그래픽의 원래 층을 구현하는 것이 원칙입니다.
2) LFL(LITHO-FREEZE-LITHO-ETCH LITHOGRAPHY-CURING-LITHOGRAPHY-ETCHING) : 화학적으로 동결되었지만 제거되지 않은 첫 번째 포토레지스트 층에 두 번째 포토레지스트 층을 추가하고 다시 포토리소그래피를 수행하여 이중 접기 구조를 형성하는 원리입니다. LELE 및 LFLF 기술의 특징은 공정이 간단하다는 것이지만, 단점은 두 리소그래피 사이에 정렬 문제가 있다는 것이며, 공정이 충분히 엄격하지 않으면 각 노광의 선폭 편차와 두 노광 사이의 오버레이 오차로 인해 패턴의 국부적인 주기적 변동이 발생합니다.
그림 16: LELE 원리
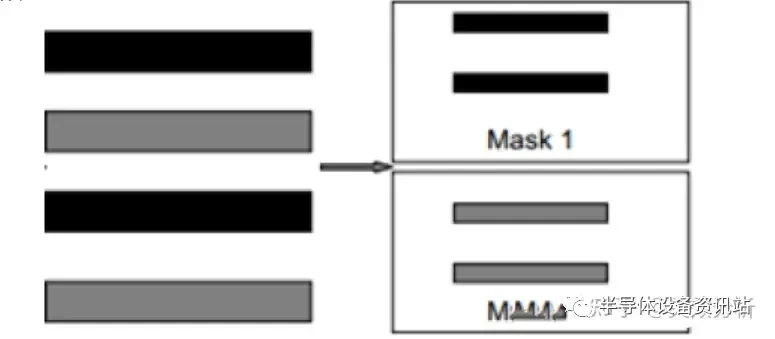
그림 17: 오버레이 오류로 인한 사이클 이동
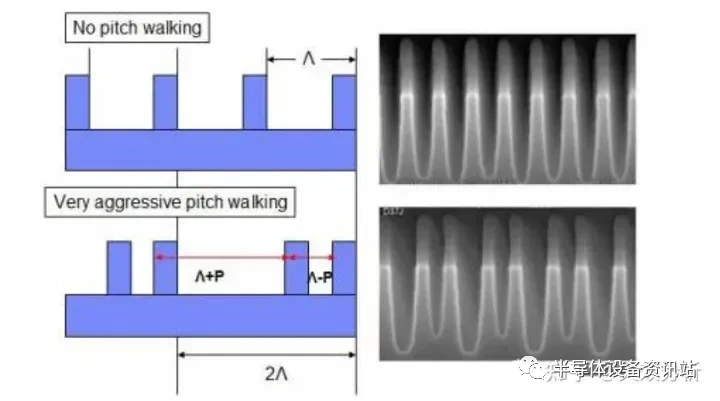
3) 측벽 패턴 전송이라고도 하는 SADP는 증착 및 에칭 기술을 사용하여 리소그래피의 정확도를 향상시킵니다: 웨이퍼에 금속 유전체층, 하드 마스크 재료 및 맨드릴 재료(희생층)를 증착하고, 코팅 포토레지스트를 스핀하고, 노출 및 현상 후 필요한 패턴을 남겨두고, 코어 맨드릴을 에칭하고, 맨드릴 주변에 스페이서 측벽 층을 증착하고, 측벽의 크기는 상호 연결선의 선 간격이며, 그 균일성은 상호 연결선 간격의 균일성을 보장하기 위해 정확하게 제어되어야 하며, 맨드릴 재료를 제거하고 측벽만 남긴 다음 측벽 패턴을 하부 마스크 층 측벽 클리어링에 에칭하고, 마스크 층 수정 패턴 후 또 다른 에칭 후 금속 유전체로 옮겨져 최종 패턴을 형성하고 선폭은 원본의 1/2에 불과하며 SADP는 4배의 정확도를 두 번 달성할 수 있습니다.
요약: 증착에 의해 형성된 측벽은 마스크로 사용되며 최종 패턴은 금속 유전체층에 에칭됩니다. 난이도: 이 과정은 측벽 침전물의 두께와 에칭 형태를 제어하는 데 매우 중요합니다.
그림 18: SAP 기술 프로세스 흐름
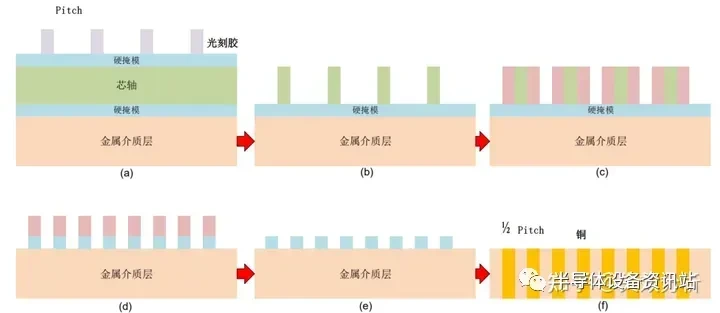
다중 노광으로 7nm 공정을 달성할 수 있지만 기술은 복잡하고 비용이 많이 듭니다: 다중 LE 또는 SADP는 7nm 공정을 달성할 수 있지만 다중 노광 기술은 에칭, 증착 및 기타 공정에 대한 기술 요구 사항을 증가시키고 사용 횟수를 증가시켜 웨이퍼 리소그래피 비용이 2-3배 증가합니다.
EUV는 sub-5nm 공정과 저렴한 비용으로 달성할 수 있습니다: 현재 EUV만이 5nm 이하를 달성할 수 있습니다. 또한, EUV를 사용하면 에칭 및 증착과 같은 공정 단계를 효과적으로 줄일 수 있으며, 공정이 간단하고 리소그래피 비용이 저렴합니다.
그림 19: 웨이퍼 리소그래피당 비용
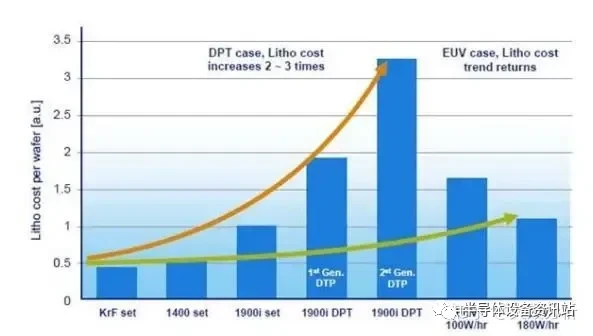
그림 20: 에칭 및 증착에 대한 수요
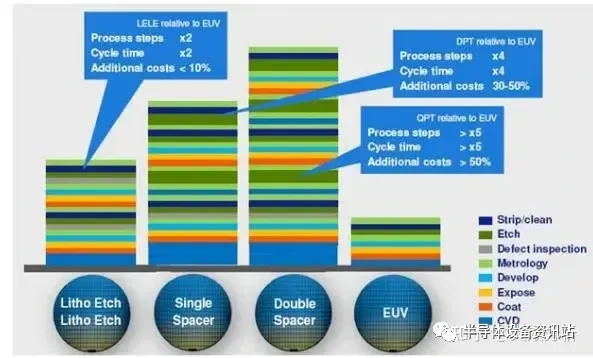
접촉식에서 EUV에 이르기까지, ASML은 절대적인 리더가 되었습니다
역사적 전환점: ASML은 이멀젼 리소그래피 기계로 시장을 독점하고 있습니다. 이멀젼 리소그래피 기술이 출현하기 전에 다양한 제조업체가 157nm 파장 기술의 연구 개발에 중점을 두었고 "이멀젼 마이크로 섀도우 기술"이 제안된 후 ASML은 TSMC와 협력하여 이멀젼 리소그래피 기계를 개발하기 시작했으며 2007년에 이멀젼 리소그래피 기계를 출시하여 성공적으로 시장을 독점했습니다. 역시 리소그래피 거인인 니콘과 캐논이 추진하는 157nm 광원 건식 리소그래피 기계는 점차 시장에서 버려져 두 회사는 번영에서 쇠퇴로 돌아섰습니다.
ASML이 지배적이며 Nikon과 Canon이 나머지 시장을 차지하고 있습니다.
1) 글로벌 리소그래피 기계 시장의 주요 경쟁자는 ASML, Nikon 및 Canon입니다. ASML은 초고급 리소그래피 기계 분야의 선두 주자로 가장 광범위한 제품을 보유하고 있습니다. 캐논의 리소그래피 기계는 주로 i-line 리소그래피 기계에 주력하고 있으며, 니콘은 EUV를 제외한 모든 기계에 관여하고 있습니다.
2) 리소그래피기의 시장 점유율은 주로 ASML, Canon, Nikon이 차지하고 있으며, 이 세 가지 비율의 관점에서 보면 2022년 ASML이 82%, Canon이 10%, Nikon이 8%를 차지할 것입니다.
그림 21: 2022년 글로벌 TOP3 리소그래피 기계 시장 점유율
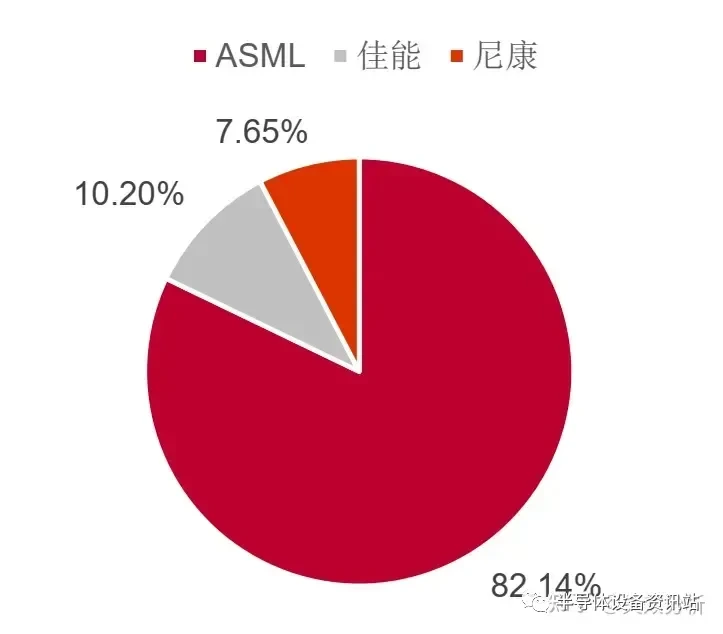
그림 22: 2022년 세계 3대 반도체 리소그래피 기계 제조업체의 출하량
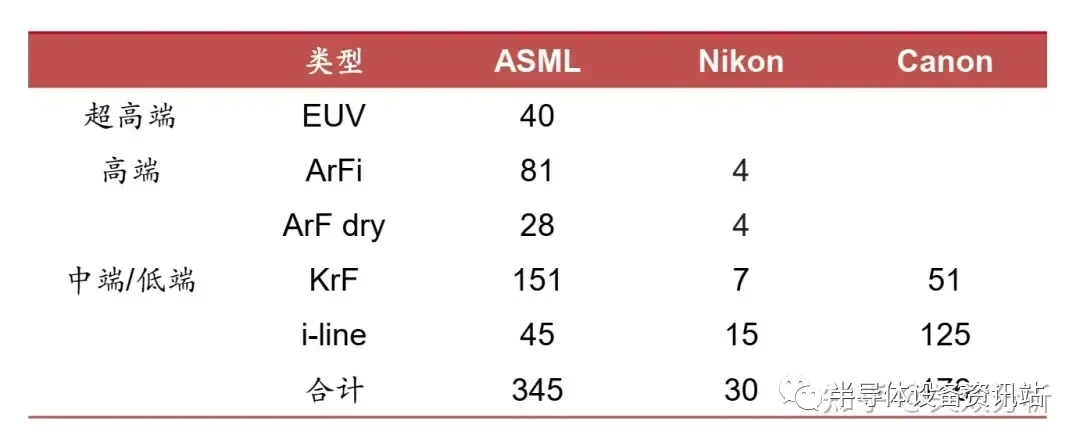
EUV 리소그래피 기계는 ASML의 매출에 가장 큰 기여를 합니다.
EUV 리소그래피 기계는 ASML의 매출에 가장 큰 기여를 합니다. ASML의 제품 판매 관점에서 볼 때, EUV 리소그래피 기계는 2022년 ASML의 프론트엔드 리소그래피 제품 판매에서 거의 50%를 차지할 것이며, ArFi의 35%가 그 뒤를 따를 것입니다. EUV와 ArFi는 하이엔드 모델로서 유닛당 가격이 더 비싸며 ASML의 주요 매출 성장 동력에 기여합니다.
KrF가 가장 많은 출하량을 보유하고 있습니다. ASML의 다양한 제품 출하량 관점에서 볼 때, 2022년 KrF가 가장 많은 출하량을 기록하고, ArFi, EUV가 그 뒤를 을 을 것입니다.
별첨 23: 유형별 ASML 리소그래피 기계 판매량(백만 유로)
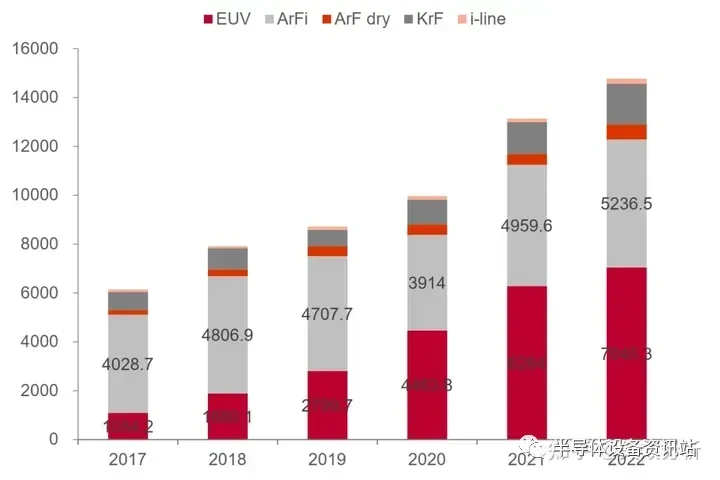
그림 24: 다양한 유형의 리소그래피 기계(단위)의 ASML 출하량
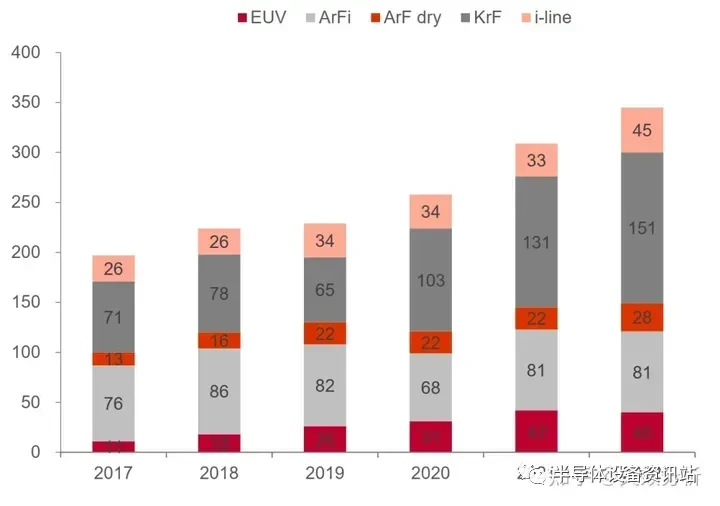
ASML은 리소그래피 기계로 세계 반도체 장비 제조업체 중 2위를 차지하고 있습니다.
ASML은 리소그래피 기계로 세계 반도체 장비 제조업체 중 2위를 차지하고 있습니다. 통계에 따르면 2021년 ASML은 217억7500만 달러의 매출로 글로벌 반도체 장비 제조업체 중 매출 순위 2위를 차지해 미국 어플라이드 머티어리얼즈에 이어 2위를 차지했다.
Exhibit 25: 2021년 세계 10대 반도체 장비 제조업체(미화 10억 달러)
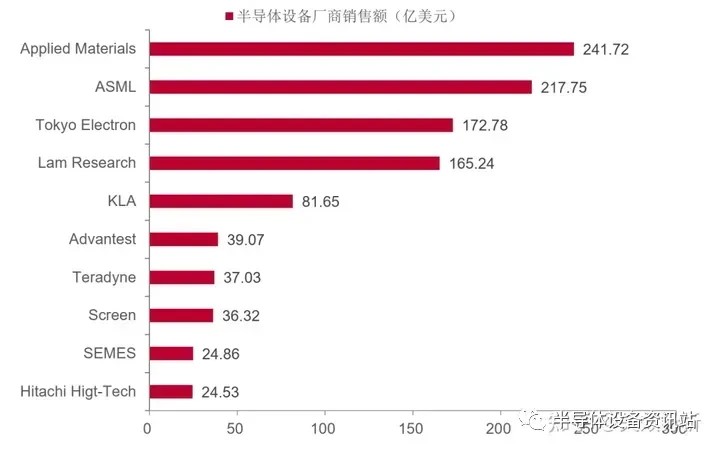
ASML은 세계 유일의 EUV 공급업체입니다.
ASML은 가장 완벽한 리소그래피 기계를 보유하고 있으며 3nm의 작은 공정으로 EUV 리소그래피 기계를 생산할 수 있는 세계 유일의 회사입니다.
1) ASML은 건식 DUV 리소그래피 기계, 침지 DUV 리소그래피 기계, EUV 리소그래피 기계를 포괄하며, EUV 리소그래피 기계를 생산할 수 있는 세계 유일의 기업으로 절대적인 우위를 점하고 있습니다.
2) 광원의 관점에서 ASML은 i-line, KrF, ArF 및 극자외선 광원을 포괄하며 최소 광원 파장은 13.5nm입니다.
3) 해상도 측면에서 ASML은 220nm, 110nm, 80nm, 38nm, 13nm 및 기타 노드를 포괄하며, EUV 리소그래피 기계는 현재 세계에서 가장 작은 해상도의 리소그래피 기계로 다중 노광 및 기타 공정 중첩 공정을 통해
5nm/3nm에 도달할 수 있습니다.
그림 26: ASML 반도체 리소그래피 기계 제품 사양
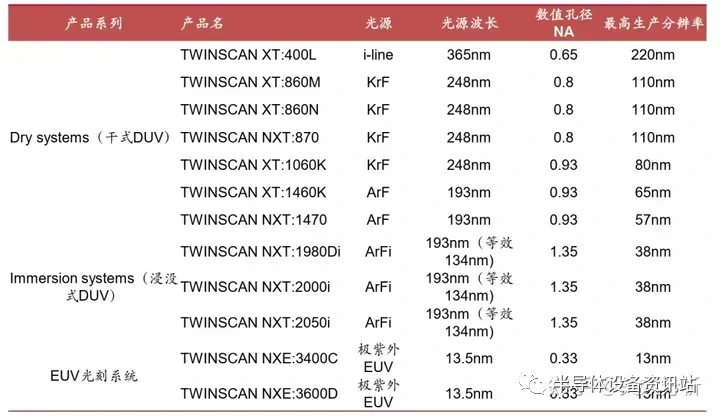
그림 27: ASML 리소그래피 기계의 역사
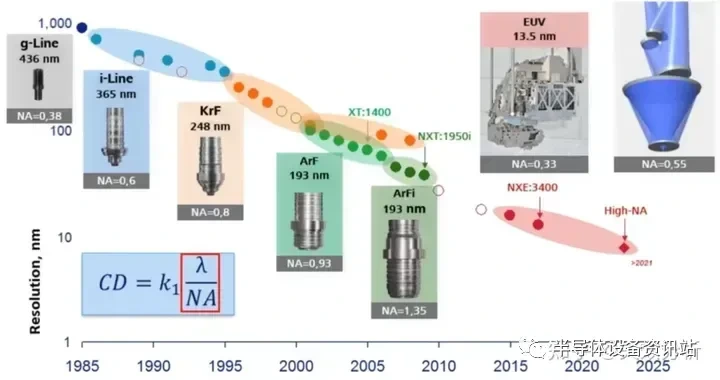
니콘 리소그래피 기계는 DUV에 중점을 둡니다.
니콘 리소그래피 기계는 DUV에 집중되어 있으며 ASML 이외의 유일한 제조업체로서 이멀젼 리소그래피 기계를 생산할 수 있습니다.
1) 종류별로 보면 니콘은 건식 DUV 리소그래피 기계와 침지 DUV 리소그래피를 보유하고 있으며, ASML 이외에 유일하게 침지 리소그래피 기계를 생산할 수 있는 메이커입니다.
2) 광원의 관점에서 Nikon은 i-line, KrF 및 ArF 광원을 커버하며 최소 광원 파장은 193nm입니다.
3) 해상도 관점에서 Nikon은 280nm, 110nm, 65nm, 38nm 및 기타 노드를 다룹니다.
별첨 28: Nikon 반도체 리소그래피 기계 사양
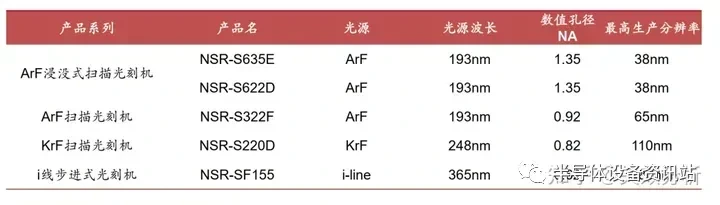
데이터 출처: 리소그래피 기계 산업 보고서, Zhongtai Securities Research Institute
캐논 리소그래피 기계는 저가형에 집중되어 있습니다
Canon 반도체 리소그래피 기계는 주로 저가형에 중점을 둡니다.
1) 타입의 관점에서 Canon은 저가형 반도체 i-line 및 KrF 리소그래피 기계를 보유하고 있으며 EUV, ArFi(immersion), ArF 및 기타 모델에는 적용되지 않습니다.
2) 광원의 관점에서 Canon은 i-line 및 KrF 광원을 커버하며 최소 광원 파장은 248nm입니다.
3) 해상도의 관점에서 Canon은 1.5미크론, 0.8미크론, 350nm, 90nm 및 기타 노드를 다룹니다.
그림 29: Canon 반도체 리소그래피 기계 사양
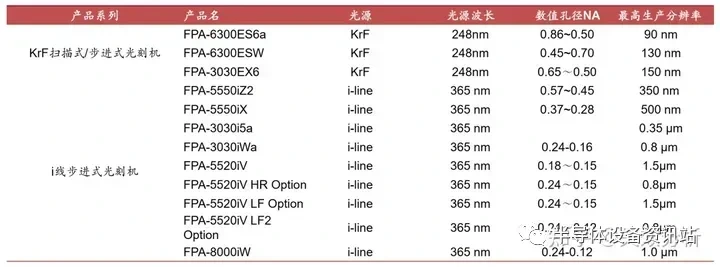
데이터 출처: 리소그래피 기계 산업 보고서, Zhongtai Securities Research Institute
리소그래피 기계: 여러 첨단 시스템의 조합이며 핵심 구성 요소는 해외 제조업체가 독점하고 있습니다.
리소그래피 기계: 인간 기술의 정점
리소그래피 기계는 프로젝션 노광 시스템입니다: 리소그래피 기계는 광원, 조명 시스템, 대물 렌즈, 공작물 테이블 및 기타 구성 요소로 조립됩니다. 칩 제조에서 포토리소그래피 기계는 패턴이 있는 포토마스크와 광학 렌즈를 통해 광선을 투사하여 회로도를 감광성 코팅이 된 실리콘 웨이퍼에 노출시킵니다. 트렌치는 노출되거나 노출되지 않은 부분을 에칭하여 형성된 다음 증착, 에칭 및 기타 공정을 수행하여 선을 형성합니다.
리소그래피 기계의 세 가지 핵심 시스템: 광원 시스템, 광학 렌즈 및 이중 테이블 시스템.
그림 30: 리소그래피 기계의 전체 구조
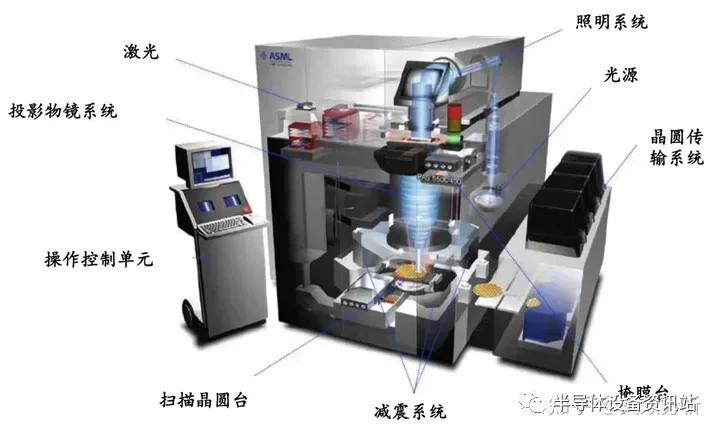
그림 31: 리소그래피 기계의 핵심 시스템 소개
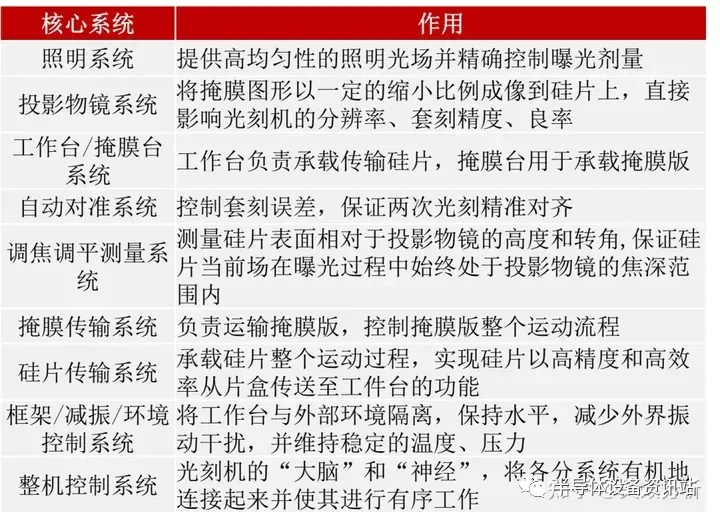
그림 32: 리소그래피 기계 구조
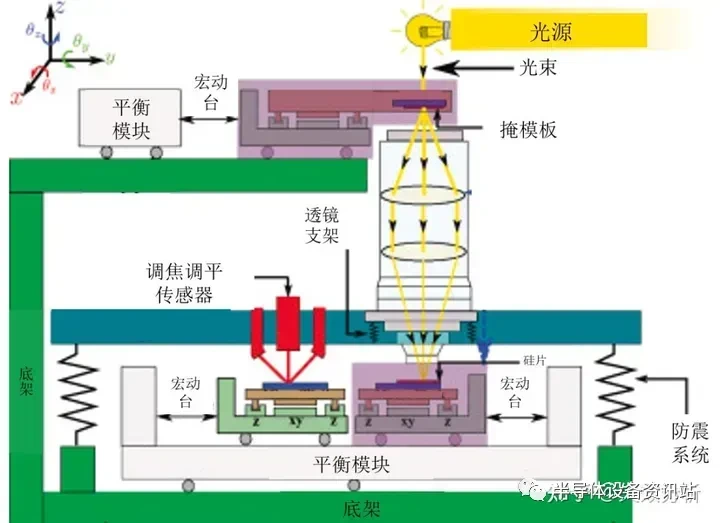
그림 33: 리소그래피 기계의 핵심 구성 요소 구조
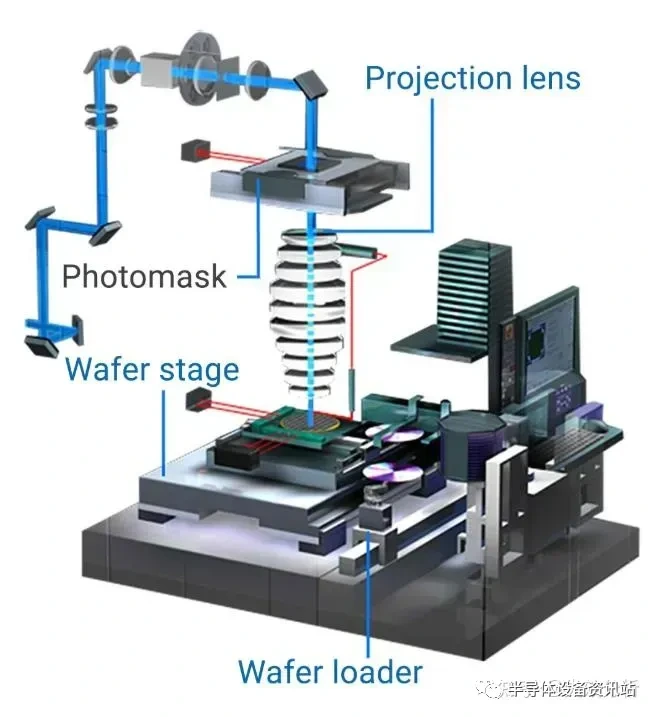
리소그래피 기계의 해상도는 광원의 파장, 개구수,
리소그래피 공정 계수 결정
리소그래피 해상도는 리소그래피 노광 시스템의 가장 중요한 기술 지표로, 광원의 파장, 개구수 및 리소그래피 공정 계수에 의해 결정됩니다. Rayleigh 기준에 따르면 해상도 공식은 R= k1 * λ/NA이며, 여기서 λ는 광원의 파장, NA는 대물렌즈의 개구수, k1은 리소그래피 공정 계수를 나타냅니다. 개구수는 렌즈와 검사 대상 물체 사이의 매체의 굴절률(n)과 조리각(2a)의 절반을 곱한 값을 나타냅니다. 공식은 NA=n*sin α입니다. n은 프로젝션 대물 렌즈 시스템의 이미지 정사각형 매체의 굴절률이고 α는 프로젝션 미러 이미지의 반조리개 각도입니다. "거울 각도"라고도 하는 조리개 각도는 렌즈의 광축에 있는 물체 점과 대물 렌즈의 전면 렌즈의 유효 직경에 의해 형성되는 각도입니다. 조리개 각도가 클수록 렌즈로 들어오는 광속이 커지며, 이는 렌즈의 유효 직경에 정비례하고 초점으로부터의 거리에 반비례합니다.
Rayleigh 기준은 회절 제한 시스템의 분해능 한계를 나타냅니다. 이상적인 이미징 시스템에서는 점의 이미지가 완벽한 점이지만 실제 광학 시스템의 렌즈는 특정 조리개 크기를 가지므로 이미지는 점이 아니라 Airy spot입니다. 서로 더 가까운 두 점의 경우 결과 점도 상대적으로 서로 가깝습니다. 두 점을 구별할 수 있는 최소 거리가 해상도입니다. 한 Airy 지점의 중심이 Rayleigh 기준이라고 하는 다른 Airy 지점의 첫 번째 최소값과 일치할 때 한계점에 도달합니다.
그림 34: 분해능 한계의 개략도
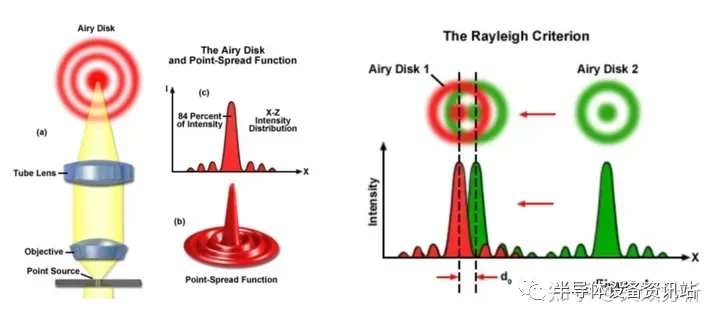
그림 35: 조리개 각도의 개략도
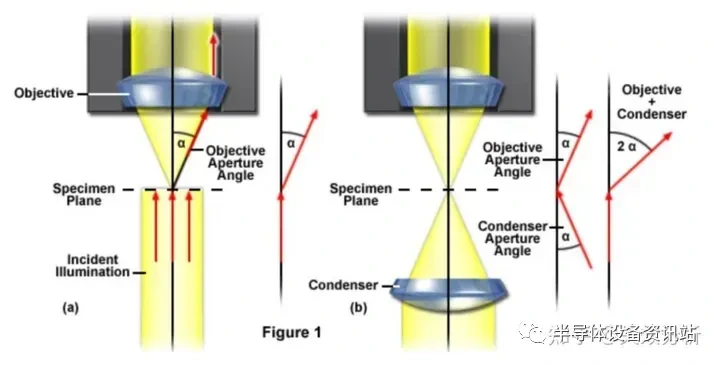
리소그래피 기계의 해상도를 향상시키는 세 가지 측면: 개구수를 늘리고 파장을 줄이며 리소그래피 공정 계수를 줄입니다. Resolution은 프로젝션 광학 시스템에 의해 웨이퍼에서 달성될 수 있는 최소 선폭을 나타냅니다. 리소그래피 기계의 해상도는 광원의 파장, 개구수 및 리소그래피 공정 계수에 의해 결정됩니다. 따라서, 해상도는 다음의 세 가지 측면에서 향상될 수 있다: 1) 투영 리소그래피 대물렌즈의 개구수를 증가시키는 단계; 2) 노출 파장을 줄이십시오. 3) 리소그래피 공정 계수를 줄입니다.
1) 프로젝션 리소그래피 대물렌즈의 개구수 증가: 한편으로는 프로젝션 렌즈 시스템을 개선하여 입사각을 높일 수 있고, 다른 한편으로는 굴절률이 높은 매체 침투 유형을 사용할 수 있습니다. aspheric surface를 사용하면 independent aberrations의 수를 늘리지 않고도 independent variables의 수를 늘릴 수 있으며, 이는 이미지 품질을 향상시키는 동시에 동일한 constraints에서 광학 부품의 수를 줄이는 데 도움이 됩니다. 비구면을 적용하면 대물렌즈 NA를 0.9로 증가시킬 수 있으며, 이는 물리적 한계(건식 리소그래피)에 가깝습니다. 이멀젼 기술의 도입으로 대물렌즈 NA를 1.1 이상으로 높일 수 있습니다(이멀젼 리소그래피). 리플렉터를 추가하면 CADIFL 구조는 이론적으로 1.35(한계)의 객관적 NA를 달성합니다. 트렌드는 (건식) 구면 거울→ 비구면
거울→ (침수) 비구면 거울→ 폴드백 미러입니다.
2) 더 짧은 노출 파장: 트랜지스터가 점점 작아지고 구성 회로가 점점 더 조밀해짐에 따라 리소그래피 기계는 더 높은 해상도를 달성해야 하므로 점점 더 짧은 파장을 가진 광원을 찾아야 합니다.
그림 36: 개구수 추세
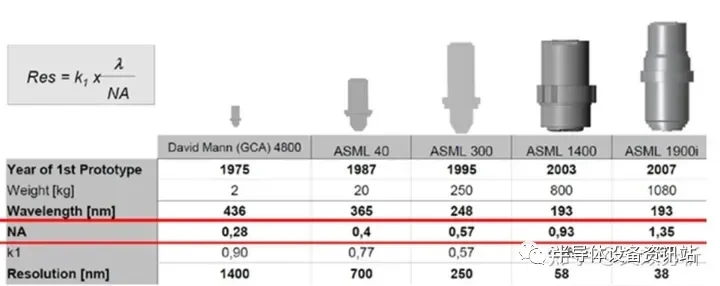
그림 37: 개구수를 늘리는 방법
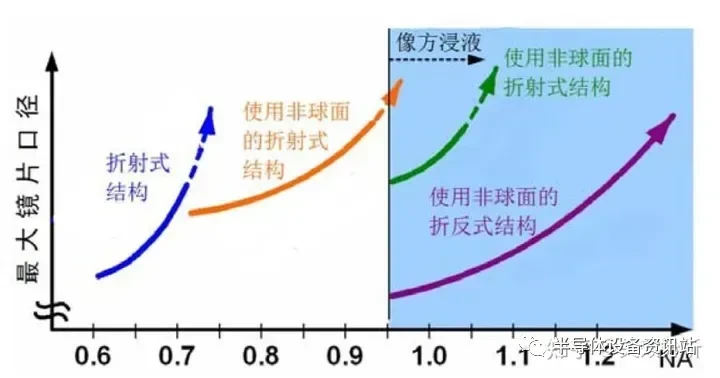
3) 리소그래피 프로세스 계수 감소: 전산 리소그래피 OPC - 이미지 왜곡을 제거하고 해상도를 향상시키기 위해 마스크에 보조 구조를 추가합니다. 축외 조명 OAI - 특수 광원을 사용함으로써 포지티브 입사광은 동일한 개구수에서 더 많은 고차 빛을 흡수하여 더 작은 구조를 노출시키고 해상도를 향상시키는 목적으로 비스듬한 입사 방법이 됩니다. 위상 편이 마스크 PSM - 두 개의 광원이 이미징 될 때 일치 부분에 간섭 효과가 발생하여 광도가 증가하여 두 광원을 효과적으로 구별 할 수 없으며, 180도 위상 변이로 광원 중 하나에서 마스크 구조를 변경하면 두 광원에서 생성 된 빛은 위상 상쇄를 생성하고 광 강도가 제거되며 두 광원을 구별 할 수 있으며 해상도를 향상시킬 수 있습니다.
공정 계수는 이론적 한계를 돌파했습니다: 단일 노광 k1에 대한 이론적 최소 한계는 약 0.25이며, 리소그래피 공정 계수는 OPC 및 다중 패턴과 같은 해상도 향상 기술의 조합을 통해 이론적 한계인 0.25를 초과했습니다.
그림 38: 포토리소그래피 OPC
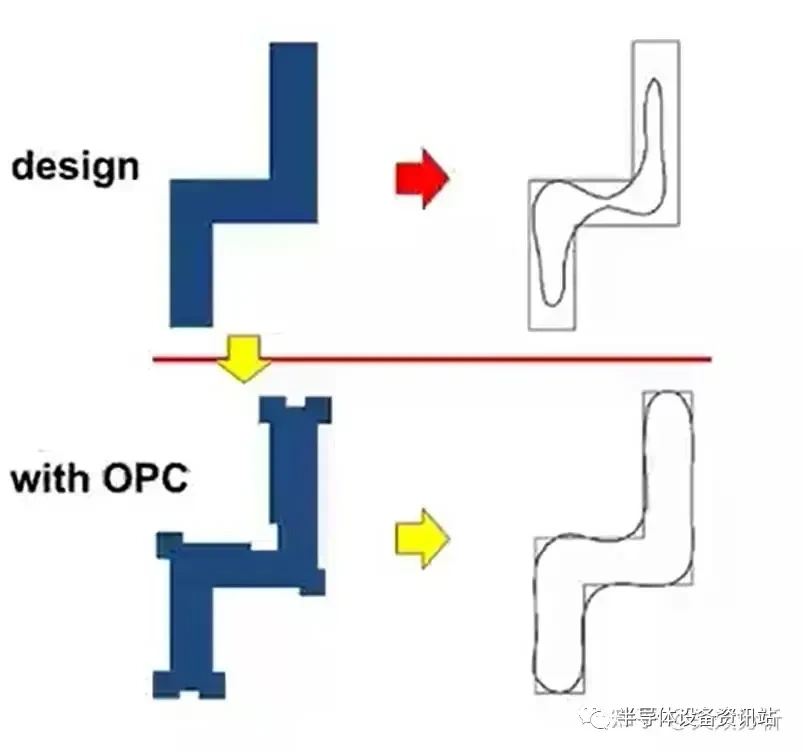
별첨 39: 축외 조명 OAI
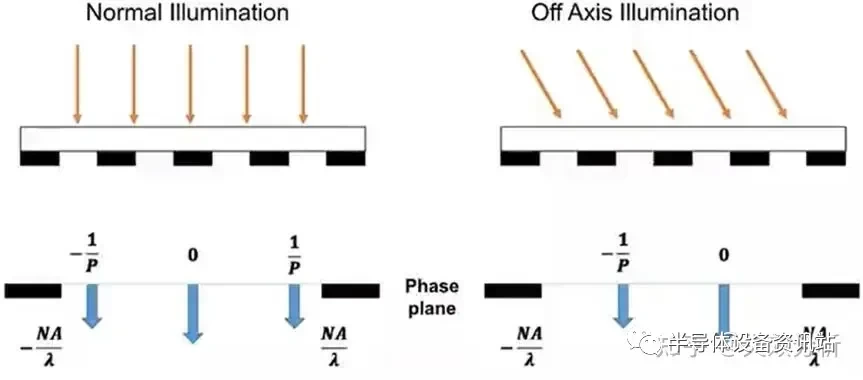
그림 40: 위상 편이 마스크 PSM
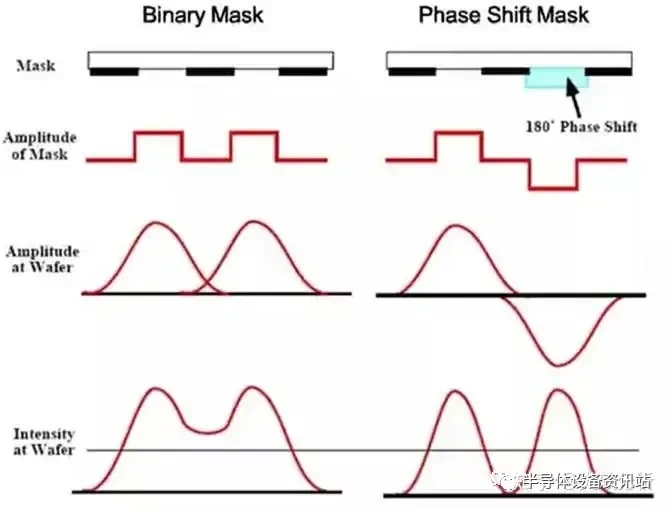
데이터 출처: 리소그래피 기계 산업 보고서, Zhongtai Securities Research Institute
광원 시스템: 에너지원, 리소그래피 공정의 주요 결정 요인
광원은 리소그래피 기계의 핵심 시스템 중 하나이며, 리소그래피 기계의 공정 능력은 먼저 광원의 파장에 따라 달라집니다.
광원은 수은 램프에서 생성되는 자외선, 심자외선, 극자외선으로 나뉘며 광원의 파장은 13.5nm로 개발되어 더 작은 칩 제조 공정을 추구하기 위해서는 광원의 파장을 지속적으로 줄여야 하며 초기 리소그래피 기계의 광원은 고압 수은 램프에서 발생하는 자외선 광원을 사용하며 고압 수은 램프는 436nm(g-line, 365nm(i-line) 파장의 자외선을 생성할 수 있습니다. KrF(248nm), ArF(193nm), F2(157nm)의 공정이 7nm 이하로 파종될 수 있는 경우 극자외선 레이저(EUV 레이저)가 필요하며, 최대 13.5nm의 매우 짧은 파장의 광원이 필요한데, 이는 레이저에서 생성할 수 없고 금속 주석에 의해 여기된 플라즈마의 고에너지 레이저 충격에 의해 생성되어야 합니다.
그림 41: 광원의 파장 전개
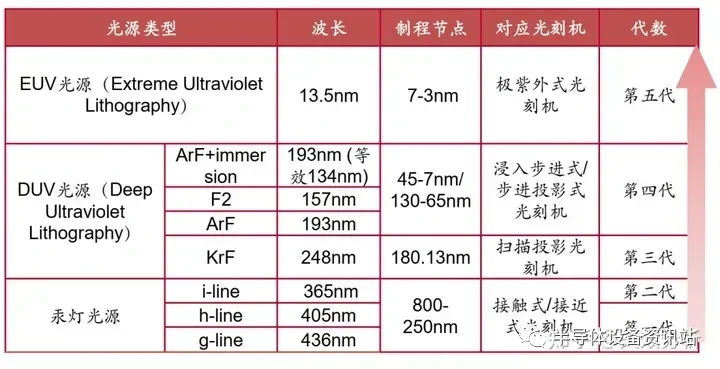
그림 42: 스펙트럼 플롯
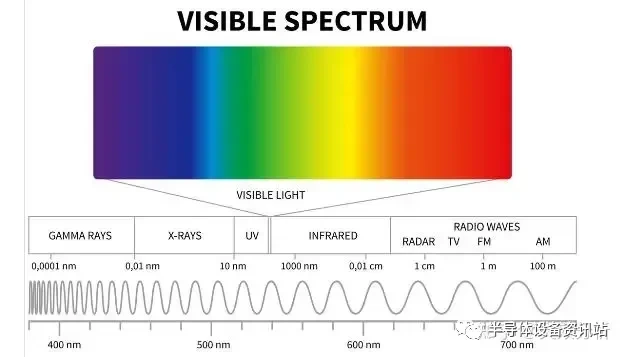
리소그래피 광원 시스템은 고압 수은 광원 제판에서 심자외선 광원, 극자외선 광원에 이르기까지 지속적으로 진화하고 있습니다.
1) 고압 수은 램프 : 가스 방전 전기 광원, 수은 증기는 에너지에 의해 여기되고 수은 원자의 가장 바깥쪽 전자는 전이하기 위해 여기되며 광자는 후퇴 후 방출됩니다. 방전관은 시동을 위한 아르곤 가스와 방전을 위한 수은으로 채워집니다.
2) 심자외선 광원 : 일반적으로 엑시머 레이저가 광원으로 사용됩니다. 엑시머 레이저 광원의 작동 매체는 일반적으로 희귀 가스 및 할로겐 가스이며, 불활성 가스는 완충액으로 채워지고, 작동 가스는 방전에 의해 여기되어 여기 상태에서 수명이 짧은 "엑시머"를 형성하고, 엑시머는 방사선 전이에 의해 자극되어 자외선 레이저 출력을 형성합니다. 엑시머 레이저는 종종 출력 에너지, 파장, 선폭 및 안정성 측면에서 이전의 수은 광원을 훨씬 능가합니다.
그림 43: 고압 수은 광원 시스템의 구조도
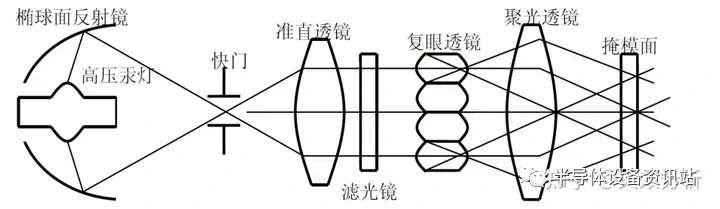
그림 44: UV 레이저 조명 시스템의 다이어그램
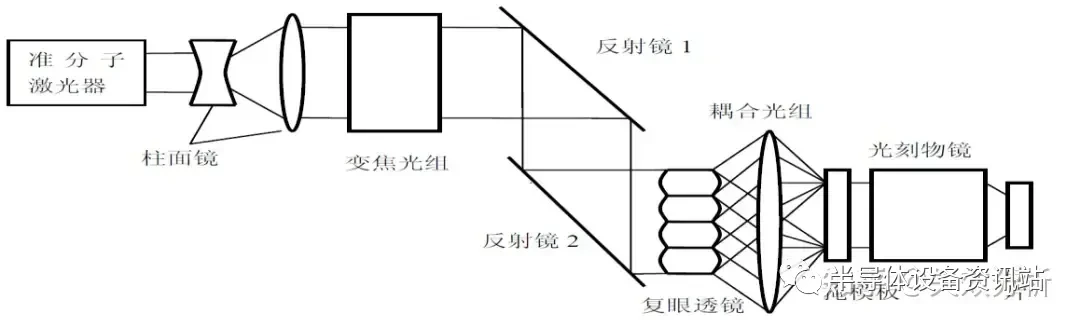
그림 45: Cymer 엑시머 레이저의 작동 원리
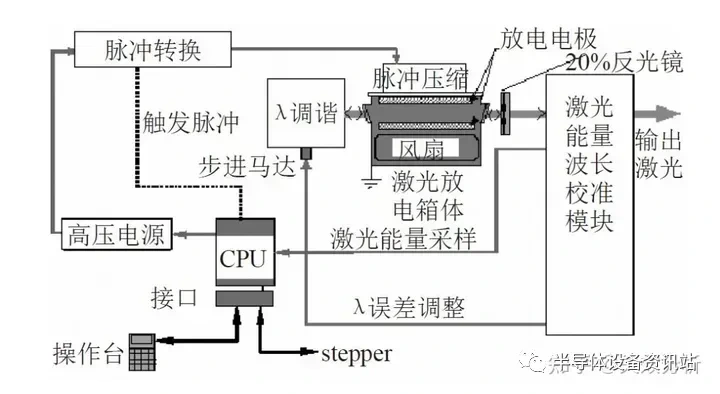
3) 극자외선 광원 : 극자외선 광원은 광생성, 집광, 스펙트럼 정제 및 균질화의 세 가지 단위로 구성됩니다. 작업 구성 요소에는 고출력 CO2 레이저, 다층 코팅 거울, 하중, 집광기, 마스크 등이 포함됩니다.
극자외선 광원의 원리: 고출력 레이저가 금속 주석을 쳐서 플라즈마를 생성하고 극자외선을 방출합니다. 직경 30미크론의 주석 방울에 고출력 이산화탄소 레이저를 두드려 주석 방울을 고출력 레이저에 의해 증발시키고 용융 주석을 높은 곳에서 초당 50,000회의 빈도로 방울당 20미크론 크기로 낙하하여 각 주석 방울을 조준하고 CO2 레이저에 의해 생성된 고에너지 레이저가 플라즈마를 히트시켜 생성함으로써 파장 13.5nm의 EUV 광을 방출합니다. 실제로 레이저는 사전 펄스와 주 펄스의 두 가지 펄스를 방출합니다. 프리 펄스는 먼저 솔더 비드를 히트시켜 올바른 모양으로 만든 다음 메인 펄스가 평평한 솔더 비드를 플라즈마로 변환하여 EUV 빛을 방출합니다.
그림 46: EUV 광원 시스템 다이어그램
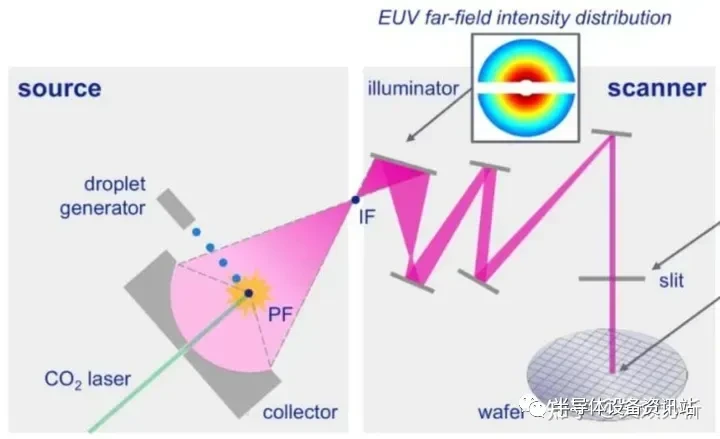
그림 47: EUV 광원 이중 펄스 방식
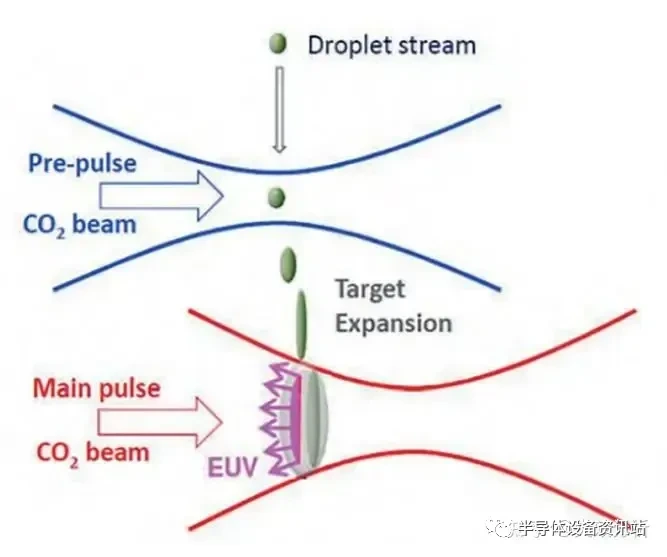
그림 48: EUV 광 생성 과정
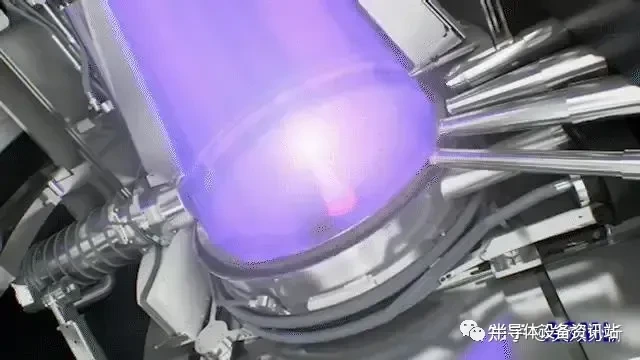
EUV 리소그래피 기계의 기술적 어려움은 주로 광원의 높은 출력에 기인합니다: 극자외선 리소그래피의 요구 사항을 충족하기 위해 광원은 다음과 같은 특성을 가져야 합니다: (1) 광원의 전력은 최대 250W이고 전력 변동이 작습니다. (2) 주파수 노이즈와 작은 상대 강도 노이즈로 좁은 레이저 선폭으로 광학 손실을 줄입니다. (3) 높은 시스템 효율. 광원 변환 속도는 결국 250와트 이상의 출력에 도달하므로 레이저의 평균 출력은 20kW에 도달해야 합니다. 레이저 빔이 매우 높은 출력으로 안정적으로 전달되기 위해서는 시스템이 매우 복잡합니다. EUV 레이저 시스템은 약 450,000개의 부품으로 구성되며 무게는 약 17톤입니다. 시드 광 생성기에서 솔더 비드까지 500미터 이상의 광학 경로를 통해 모든 구성 요소에 대한 요구 사항이 매우 까다롭습니다.
기가포톤(EUV 광원 공급 업체 중 하나) 최대 27kW의 레이저: 기가포톤은 설립 이래 ASML, Nikon, Canon에 레이저 광원을 공급하고 있습니다. 총 3개의 EUV 광원, 즉 Proto#1, Proto#12 및 Pilot#1이 설계되었으며, 그 중 Pilot#1은 레이저 출력 27kw, 출력 출력 250W의 상용 제품입니다. 현재 EUV 광원을 생산할 수 있는 회사는 미국의 Cymer와 일본의 Gigaphoton, 단 두 곳뿐입니다.
Exhibit 49: 기가포톤 EUV 광원 제품 파라미터
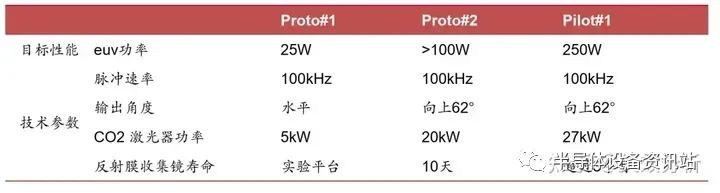
노출 시스템: 조명 시스템 + 프로젝션 대물렌즈
노광 시스템: 노광 시스템은 조명 시스템(광원 처리)과 프로젝션 대물렌즈(고해상도 이미징)로 구성되며 리소그래피 기계에서 가장 비싸고 복잡한 구성 요소 중 하나입니다. 대물렌즈의 성능은 리소그래피기의 핵심 부품인 리소그래피기의 선폭과 오버레이 정확도를 결정하며, 그 기술 수준은 주로 리소그래피 기계의 기술 수준을 나타냅니다.
그림 49: 리소그래피 기계 조명 및 프로젝션 대물렌즈 시스템의 워크플로우 다이어그램
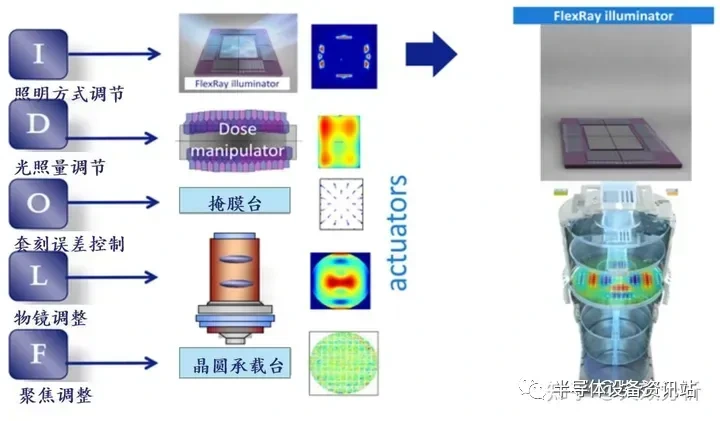
조명 시스템: 광원의 고품질 처리를 위한 핵심
조명 시스템은 특정 광, 각도 스펙트럼 및 강도 분포를 가진 프로젝션 대물렌즈 이미징을 위한 조명 조명 필드를 제공합니다. 조명 시스템은 광원과 프로젝션 대물 렌즈 사이에 위치하며 복잡한 비이미징 광학 시스템입니다. 조명 시스템의 주요 기능은 특정 광 각도 스펙트럼 및 강도 분포를 가진 프로젝션 대물렌즈 이미징을 위한 조명 필드를 제공하는 것입니다. 조명 시스템에는 빔 처리, 동공 형성, 에너지 감지, 라이트 필드 균질화, 릴레이 이미징 및 편광 조명과 같은 장치가 포함됩니다.
그림 50: 광학 시스템의 원리
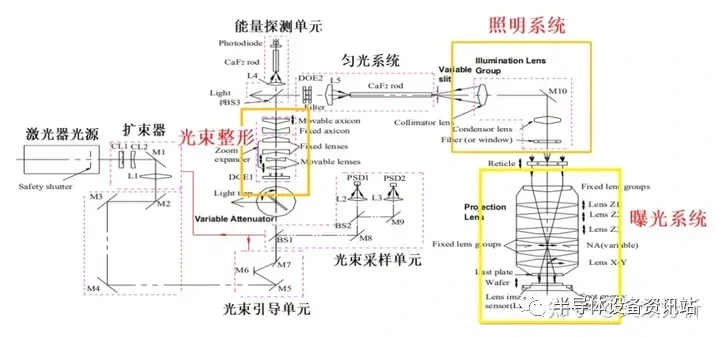
조명 시스템 구성 요소: 1) 빔 처리 장치: 주로 빔 확장, 빔 전송, 빔 안정화 및 투과율 제어 기능을 실현하기 위해 광원과 연결되며, 여기서 빔 안정화는 빔 모니터링과 빔 조향의 두 부분으로 구성됩니다. 2) 동공 형성 장치: 리소그래피 기계는 리소그래피 해상도를 향상시키고 이미징 대비를 개선하기 위해 다양한 마스크 구조에 대해 다른 조명 모드를 채택해야 합니다. 동공 형성 장치는 광학 장치를 통해 레이저 빔의 강도 또는 위상 분포를 조절하여 다양한 조명 모드를 달성합니다. 3) Light field homogenization unit: 특정 강도 분포를 가진 조명 light field를 생성하는 데 사용됩니다. 투과형 fly-eye 마이크로렌즈 어레이가 도입되고 각 마이크로렌즈는 빔 확장 시준 후 광원을 여러 개의 서브 광원으로 나누고 각 서브 광원은 Kohler 조명 렌즈 그룹을 통과한 후 마스크 표면에 중첩되어 매우 균일한 조명 라이트 필드를 달성합니다. 4) 릴레이 미러: 마스크 표면에 균일한 빔 강도로 엄격한 조명 영역을 형성하고 마스크 평면의 중간 평면을 정확하게 이미지화합니다.
그림 51: 조명 시스템 구조
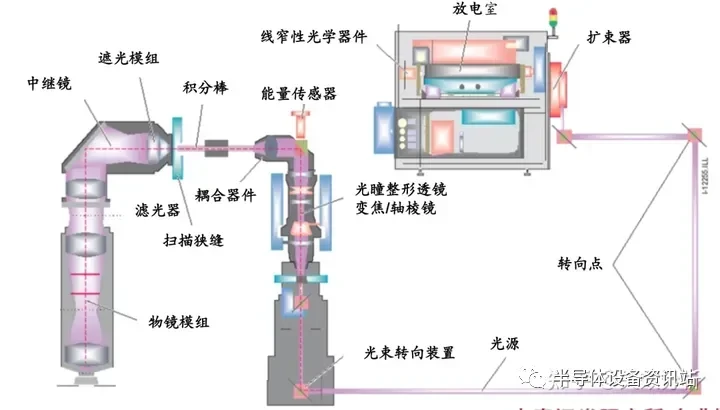
조명 시스템의 기술적 어려움: 웨이퍼에서 빛 에너지를 완벽하게 이미지화하기 위해서는 고품질 처리가 필요합니다.
1) 광 균일성 향상: 리소그래피는 앞뒤 스캔으로 이미지화해야 하며 광 스트립의 에너지는 어느 위치에서나 일정해야 합니다. 빛의 균일성을 향상시키기 위해 거울을 통해 여러 번 반사해야 합니다.
2) 스캐닝 스트립의 개폐 제어: 웨이퍼에서 노광 장치의 모든 위치는 동일한 양의 빛을 받아야 하므로 스캐닝 스트립은 열고 닫을 수 있어야 합니다.
3) 빛의 모양을 조정하기 위해서는 동공 형성 기술이 필요합니다 : 원형, 고리, 2 차 및 4 차 광원과 같은 다양한 조명 방법, 리소그래피 기계의 해상도가 다릅니다. 예를 들어, 빛이 마스크의 패턴을 통과할 때 회절 효과가 발생하며, 선폭이 작을수록 회절 각도가 커지고, 1차 회절 빛은 투영 목표를 넘어 이미징할 수 없습니다. 스포트 라이트의 모양이 링 라이트 또는 다른 모양으로 변경되면 1차 회절광이 대물 렌즈에 포함될 수 있고 이미지 콘트라스트가 선명합니다.
그림 52: 회절광은 이미징할 수 없습니다.
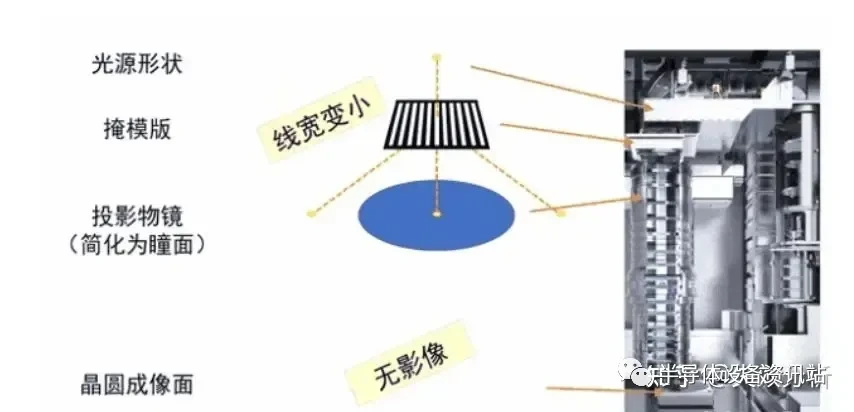
그림 53: 링 라이트 이미징
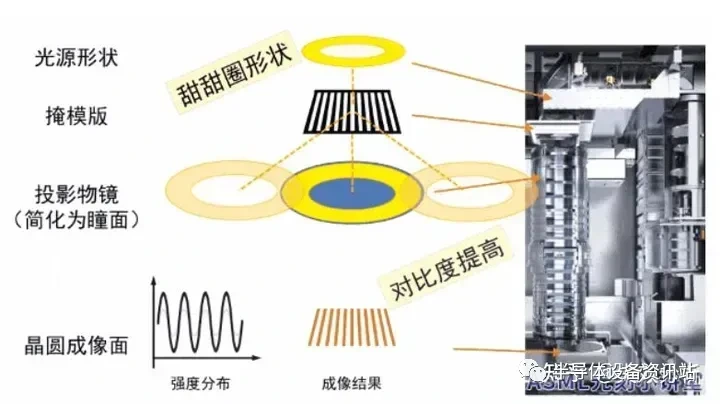
동공 형성 장치는 조명 시스템에서 기술적으로 어려운 구성 요소이며 주요 기술은 회절 광학 요소(DOE)를 기반으로 하는 동공 형성 기술과 MMA(Micro-Mirror Array)를 기반으로 하는 자유 동공 형성 기술입니다.
회절 광학 소자(DOE)의 동공 형성: 동공 형성 장치에는 주로 회절 광학 소자, 줌 푸리에 변환 미러 세트, 원뿔형 미러 세트 및 동공 보정기가 포함됩니다. 회절 광학 요소는 조명된 동공의 각도 변조를 구현하는 데 사용되며 푸리에 변환 미러 그룹과 원뿔 미러 그룹은 조명된 동공의 방사형 변조를 구현하는 데 사용됩니다. 단점: 1개의 회절 광학 소자로 1개의 조명 모드만 달성할 수 있습니다.
MMA(Micro-Mirror Array)의 Free pupil shaping: 주로 energy equalization components, beam segmentation components, micro-mirror arrays 및 Fourier transform mirror group으로 구성됩니다. 핵심 장치는 지속적으로 조정 가능한 2차원 회전 각도를 가진 수천 개의 마이크로 미러로 구성된 마이크로 미러 어레이이며, 모든 조명 모드는 마이크로 미러 어레이의 각도 위치 분포를 조정하여 실현할 수 있습니다.
그림 54: 회절 광학 소자를 기반으로 한 동공 형성 기법
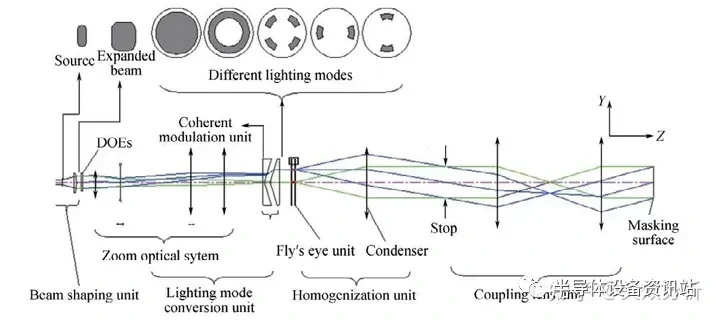
그림 55: 마이크로미러 어레이를 기반으로 한 동공 형성 기법
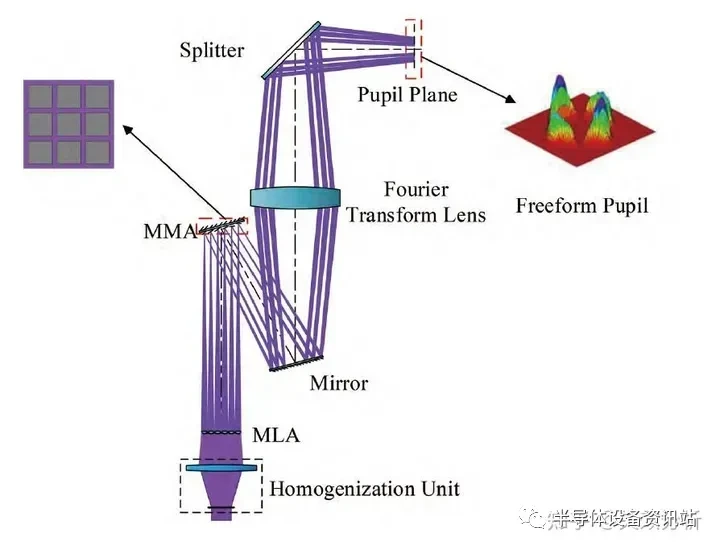
프로젝션 대물 렌즈 시스템: 선폭에서 중요한 역할을 하는 정밀한 이미징
프로젝션 대물렌즈는 정확한 이미징의 핵심입니다: 프로젝션 대물렌즈는 조명 모듈에서 방출되는 1차 회절광을 대물렌즈로 가져온 다음 마스크의 회로 패턴을 줄여 웨이퍼에 이미지를 초점을 맞추고 광학 오류를 보정합니다. 프로젝션 대물렌즈는 주로 여러 개의 렌즈로 구성됩니다. 해상도 요구 사항의 지속적인 개선으로 리소그래피 기계의 프로젝션 대물 렌즈의 구조는 점점 더 복잡해지고 있으며 광학 재료, 광학 가공 및 광학 코팅에 대한 요구 사항은 현재 산업 수준의 한계에 도달했으며, 이는 리소그래피 기계에서 가장 높은 기술 장벽을 가진 구성 요소 중 하나입니다.
projection objective lens의 구조는 굴절형과 catadioptric type으로 나뉩니다: 1) 굴절형: 광학 요소가 대칭으로 회전하고 동일한 광축을 따라 정렬되고 시야는 광축의 중심에 위치하며 구조가 간단하고 조정하기 쉽습니다. 2) 카타디옵터(Catadiopter, NA>1.1): 거울은 양의 힘과 음의 시야 곡률을 가지며 전통적인 "허리 배" 구조에 의존하지 않으며 더 작은 조리개를 가진 더 적은 수의 광학 요소를 사용하여 시야 곡률 보정을 충족하여 특정 목표 크기 한계 내에서 더 큰 NA를 얻습니다.
대물 렌즈의 특징은 대구경, 다중 렌즈 및 가동 렌즈입니다. 1) 대물 렌즈의 대구경: ASML DUV 리소그래피 기계에서 고급 모델의 투영 대물 렌즈의 직경은 40cm 이상이며 투영 대물 렌즈의 직경을 늘리면 개구수가 증가하여 리소그래피 기계의 해상도가 향상될 수 있습니다. 2) 다중 렌즈 조합 : ASML DUV 리소그래피 기계의 프로젝션 대물 렌즈의 높이는 1 미터 이상이며 렌즈 수는 15 개 이상입니다. 카메라와 마찬가지로 단일 렌즈의 광학적 특성으로 인해 이미지 왜곡이 발생할 수 있으며 이미지 왜곡을 보정하기 위해 렌즈를 결합해야 합니다. 3) Movable lenses: Moving lens는 렌즈 조립 및 리소그래피 생산으로 인한 다양한 aberrations를 제거하는 데 사용됩니다. Movable lens는 수직 보정, 기울기 보정 및 다방향 보정을 커버합니다.
그림 56: 일반적인 굴절 투영 대물렌즈의 개략도
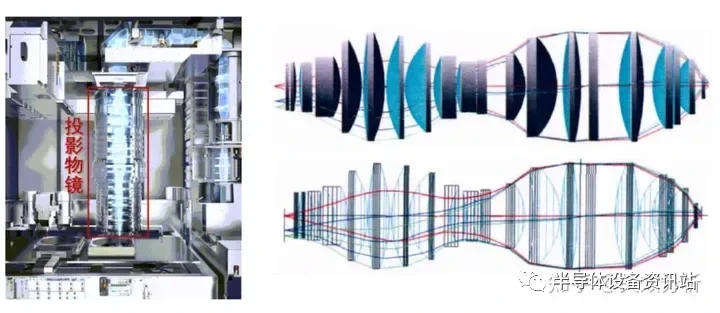
그림 57: catadioptric projection objective의 개략도
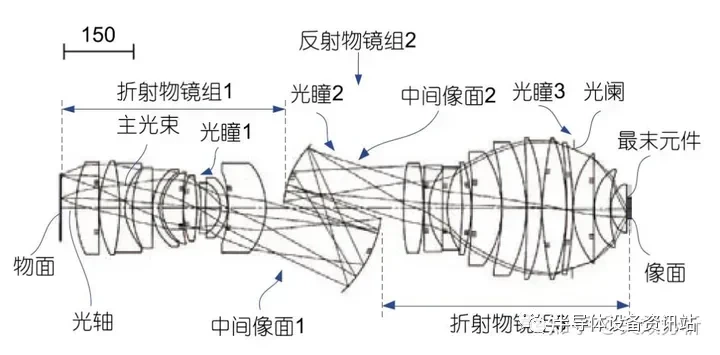
프로젝션 대물 렌즈의 기술적 어려움: 높은 수차 조정 요구 사항 및 정밀한 공정.
1) 수차 조정에 대한 높은 요구 사항: 파동 수차는 실제 파동 표면과 이상적인 파동 표면 사이의 편차입니다: 빛이 매체에서 전파될 때 물체 지점에서 방출되는 동심원 빔은 구형파와 동일하고 구형파가 광학 시스템을 통과할 때 곡률이 변경됩니다. 이상적인 광학 시스템이라면 또 다른 구형파를 형성할 것입니다. 그러나 실제 광학 시스템에서는 투영 대물 렌즈의 재료, 특성, 두께, 거칠기, 환경 및 기타 요인의 영향을 받으며 투영 대물 렌즈가 방출된 후 파동 표면이 변형됩니다. 실제 파면 표면과 이상적인 파면 사이에 발생하는 편차를 파동 수차라고 합니다. 파수차는 리소그래피 기계의 이미징 품질과 해상도에 직접적인 영향을 미치므로 리소그래피 기계의 투영 대물 렌즈 시스템은 수차를 보정해야 합니다.
그림 58: 수차의 개략도
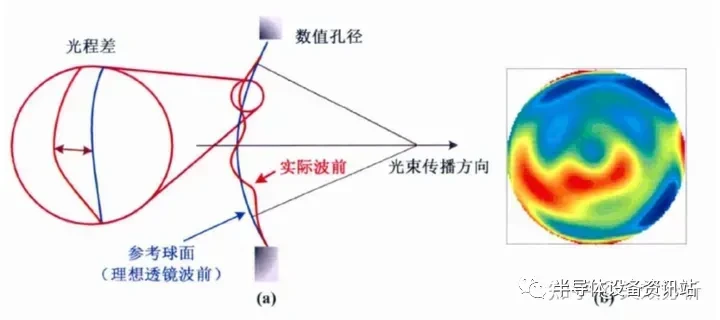
그림 59: 리소그래피 기계 이미징 공정
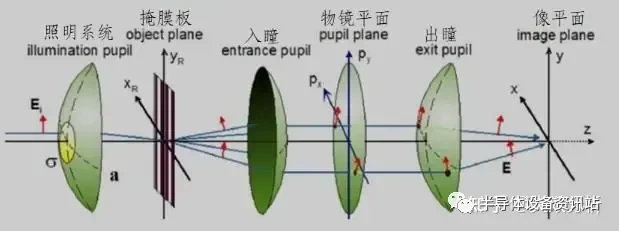
1) 수차 조정에 대한 높은 요구 사항:
수차를 더 잘 조정하기 위해 대물 렌즈의 개발 추세는 "이중 허리"에서 "단일 허리"로의 및 비구면 렌즈 및 반사 렌즈의 도입입니다.
"Double waist"에서 "Single waist"로: 필드 곡률 보정을 달성하기 위해 프로젝션 대물 렌즈는 "waist belly" 구조를 채택합니다. 비구면 수의 증가에 따라 더블 웨이스트 구조의 구조는 점차 "1.5 허리 구조"에서 "싱글 웨이스트 구조"로 바뀌고 광학 요소의 수가 감소했습니다.
비구면 렌즈: NA가 0.75보다 크면 비구면 렌즈가 도입됩니다.
이유: 한편으로는, 글로벌 구조를 채택하면 NA가 증가함에 따라 광학 소자의 조리개 크기와 부피가 급격히 증가합니다. 반면에, 대물렌즈 투영 대물렌즈의 NA가 증가함에 따라 설계 복잡성이 증가하고, 해상도가 향상되며, 이미징 품질 요구 사항이 더욱 향상됩니다.
반사 렌즈 소개: NA가 1.1보다 크면 catadioptric projection lithography objective가 필요합니다. 오목한 반사 요소를 추가합니다. 오목한 표면은 양의 광력을 가지며 필드 곡률에 대한 기여도는 음수이며 오목 거울은 필드 곡률을 잘 수정할 수 있습니다.
ASML DUV 하이엔드 프로젝션 대물렌즈의 수차는 ≤2nm입니다. 고급 SLR 렌즈의 수차는 최대 200+ nm에 도달할 수 있는 반면 ASML DUV 고급 프로젝션 대물렌즈의 수차는 ≤2nm이므로 리소그래피 기계 렌즈의 평탄도가 매우 높습니다.
2) 정확한 공정 : 리소그래피 기계에 필요한 경면 마감이 매우 높기 때문에 최고 정밀 연삭기와 최고의 렌즈 연마재가 필요하며 최고의 숙련공이 필요합니다. 광학 렌즈의 생산 공정에서 CCOS 연마에만 초정밀 연마와 소형 연삭 헤드 연마, 응력 디스크 연마, 자기 유변 연마 및 이온 빔 연마와 같은 어려운 공정이 포함됩니다. ZEISS에서 생산하는 최신 세대의 EUV 리소그래피 미러는 최대 직경 1.2m, 표면 정확도 0.12나노미터, 표면 거칠기 20피코미터(0.02나노미터)로 원자 수준의 평탄도를 달성합니다.
그림 60: 프로젝션 대물렌즈와 고급 SLR 렌즈의 픽셀 차이
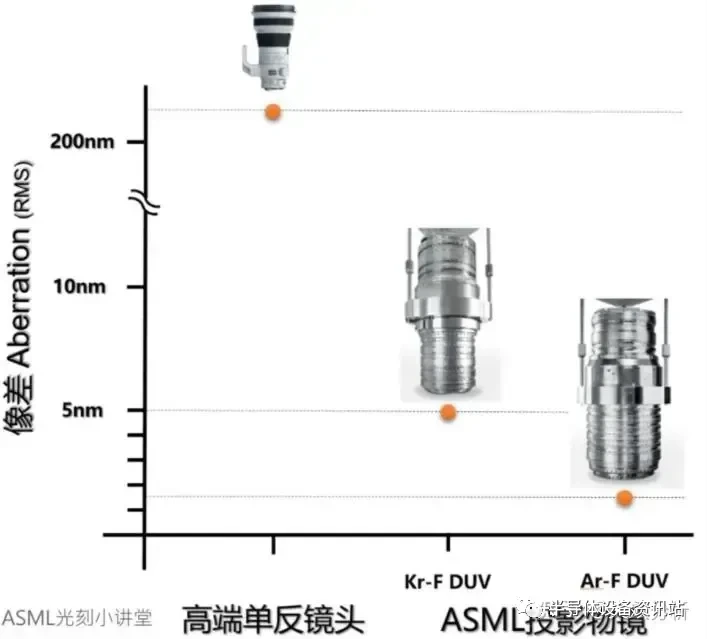
그림 61: ZEISS 대물렌즈 매개변수
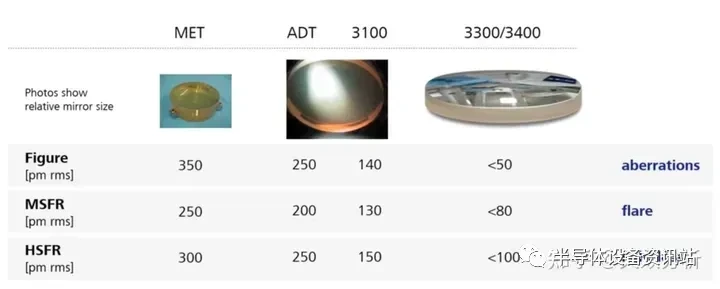
듀얼 테이블 시스템: 정확한 정렬 + 리소그래피 기계 처리량의 핵심
리소그래피 기계의 이중 작업대는 동시에 독립적으로 작동하는 두 개의 공작물 테이블로 구성되며 스텝 이동, 노출 스캐닝, 정렬 스캐닝, 실리콘 웨이퍼 로딩 및 언로딩 등의 기능을 완료하는 역할을 합니다.
듀얼 테이블 워크플로우: 작업대는 1번과 2번으로 나뉘고, 2번 공작물 스테이지는 대물렌즈 아래에 위치하며, 웨이퍼는 수평을 맞추고 초점을 맞추고, 노출시키고, 조각하는 반면, 1번 단계는 조각할 웨이퍼를 로딩 및 언로딩하는 데 사용됩니다. 2) 2번 테이블이 완성되면 공작물 테이블 시스템을 교체하고 1번 공작물 테이블을 제판용 대물렌즈 하단으로 변경하고 2번 테이블을 상부 및 하부 필름에 사용하여 리소그래피 기계의 효율적인 생산을 실현합니다. 특징 : 원래의 단일 테이블과 비교하여 이중 작업대의 효율성은 35 % 증가하고 정확도는 10 % 증가하여 리소그래피 기계의 생산 능력을 효과적으로 향상시킵니다.
그림 62: 트윈 작업대
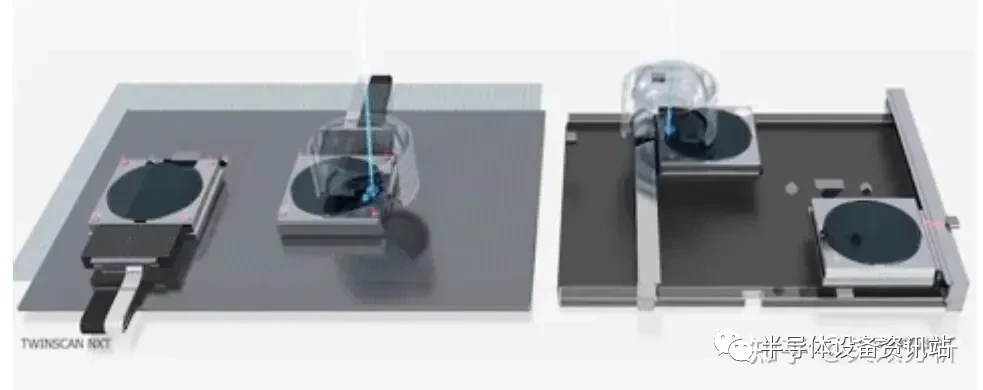
그림 63: 2테이블 시스템의 구조와 테이블 변경 프로세스
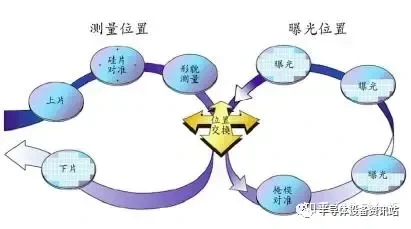
이중 작업대의 기술적 어려움: 빠른 속도, 높은 정렬 정확도 및 안정적인 움직임이 필요합니다.
1) 빠른 속도: 현재 가장 진보된 DUV 리소그래피 기계인 웨이퍼의 리소그래피 생산 속도는 300개/h이고 한 이미지 단위의 노출 이미징은 약 0.1초이며, 이 이미징 속도를 달성하려면 웨이퍼 플랫폼이 최대 7g의 고속으로 이동해야 합니다. 7g의 가속은 F1 자동차의 2.5초에 비해 0.4에서 100km/h까지 가속하는 데 약 2.5초가 걸린다는 것을 의미합니다.
2) 정확한 정렬: 직면한 어려움은 거대한 변화입니다 - 칩 제조는 층별로 적층되어야 하며 각 겹침의 오류를 오버레이 정확도라고 하며 이는 1-2nm가 되어야 합니다. 웨이퍼는 전송 모듈에서 웨이퍼 플랫폼으로 이동하며, 이로 인해 일반적으로 수천 나노미터 범위의 기계적 오류가 발생합니다. 고도 차이 - 프로젝션 대물 렌즈가 너무 크고 초점 포인트 위와 아래의 허용 가능한 이미지 범위가 100nm 미만입니다. 웨이퍼 표면이 고르지 않고 웨이퍼 플랫폼의 높이 차이가 누적되며 웨이퍼 표면의 다른 위치에서 포토레지스트 높이는 500-1000nm 다를 수 있습니다. 따라서 각 노출 전에 각 웨이퍼에 대해 정확한 측정을 수행하고 웨이퍼의 각 부분의 나노미터 수준의 작은 오류를 차단하고 노출 단계에서 실시간으로 수정해야 합니다.
3) 안정적인 모션 : 안정적인 모션 - 밸런스 웨이퍼 플랫폼에 의해 프레임에 가해지는 반력을 흡수하기 위해 밸런스 질량을 사용하여 전체 기계가 완전히 정지하도록합니다. 안정적인 포지셔닝 – 측정 완료 후 매우 짧은 노출 시간 내에 웨이퍼를 완벽하게 포지셔닝하기 위해 ASML 리소그래피 기계는 0.06나노미터의 정확도를 가진 센서를 구현하여 정확한 포지셔닝을 확인할 수 있습니다. 안정적인 작동 - 마모를 줄이기 위해 웨이퍼 플랫폼은 서스펜션 이동 모드를 채택하여 매우 빠른 이동과 장기적으로 안정적인 작동을 달성합니다.
별첨 64: TWINSCAN의 트윈 스테이지 구조 개략도

그림 65: 웨이퍼 플랫폼
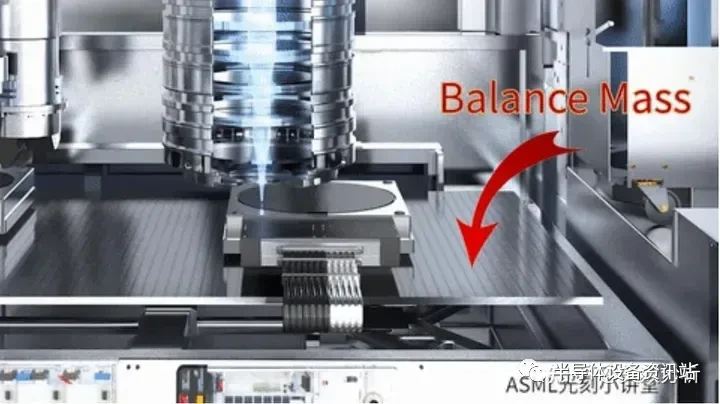
공작물 테이블의 안정적인 위치 지정과 정확한 정렬을 보장하기 위해. 격자 자, TIS 센서 등을 사용해야 합니다.
엔코더는 테이블의 위치 지정에 사용됩니다. 변위 측정 센서에는 레이저 간섭계와 격자 자가 있으며 레이저 간섭계의 환경에 대한 민감도가 높기 때문에 현재 고급 모델은 격자 자를 사용합니다. 원리: 레이저 광원은 서로 수직인 안정적인 선형 편광 방향으로 이중 주파수 레이저를 출력하고, 한 빔은 광전 감지 회로에 의해 기준 차이 주파수 신호로 수신되고, 다른 빔은 격자 스케일로 전송되어 격자 도플러 효과 및 광학 간섭 원리에 따라 변위 측정을 실현합니다.
TIS 시스템은 마스크 테이블과 웨이퍼 테이블 사이의 정렬에 사용됩니다. TIS 시스템은 (1) 마스크 테이블에 설치된 TIS 로고(Dense lines of light transmission)로 구성됩니다. (2) 웨이퍼 테이블의 TIS 센서. TIS 로고는 광학 이미징 렌즈 시스템을 통해 웨이퍼 테이블에 투사됩니다. 웨이퍼 테이블 상의 TIS 센서는 TIS 마크 이미지 강도의 공간 분포를 측정하고, 웨이퍼 테이블에 대한 마스크 테이블 상의 TIS 마크의 위치를 계산한다. TIS 시스템은 또한 projection lens 시스템의 수차와 이미징 시스템의 왜곡을 추가로 측정할 수 있습니다.
그림 66: 엔코더 스케일 측정 시스템의 개략도
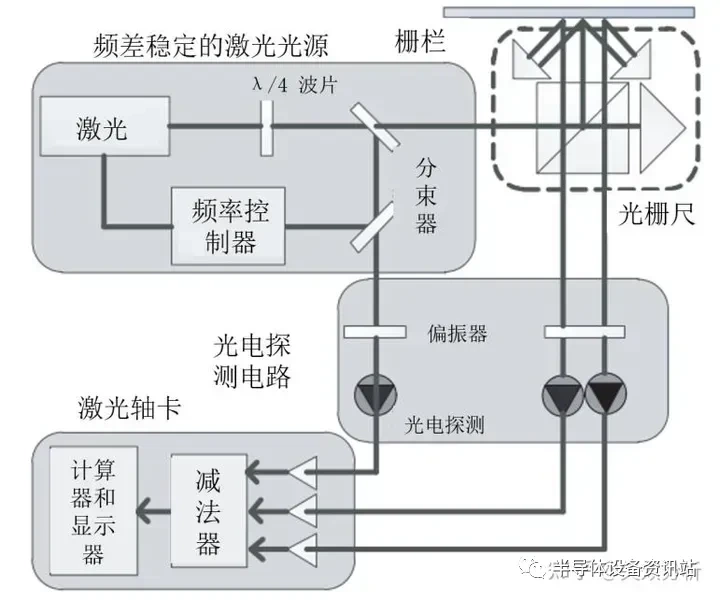
그림 67: TIS 정렬 시스템의 개략도
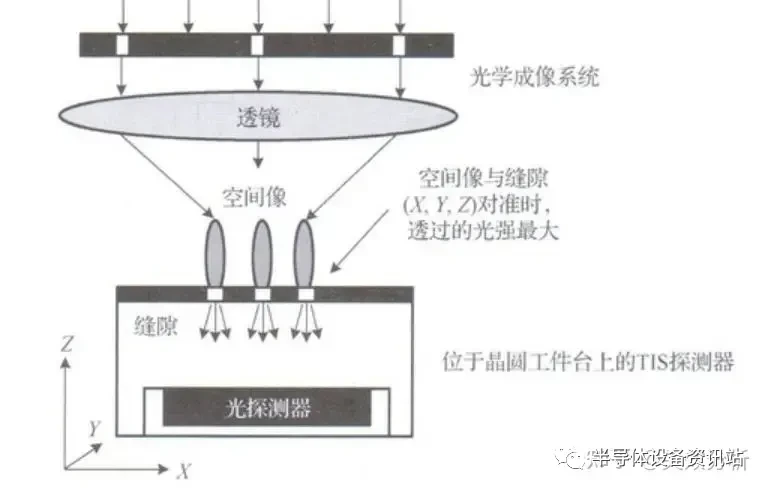
'Semiconductor' 카테고리의 다른 글
Lam Research 제품 라이브러리 - 2부 (0) | 2025.01.23 |
---|---|
Lam Research 제품 라이브러리(벡터, ALTUS, SPEED...) - 1부 (0) | 2025.01.23 |
Rohm, Wolfspeed, Sumitomo Electric 실리콘 카바이드 투자 변경 (0) | 2025.01.23 |
삼성전자, LG이노텍, 네그(Neg) 등 유리 기판 생산 및 개발 최신 트렌드 개발 !!! (0) | 2025.01.23 |
2024 연도 매출 보고 - SK 하이닉스 (0) | 2025.01.23 |
댓글